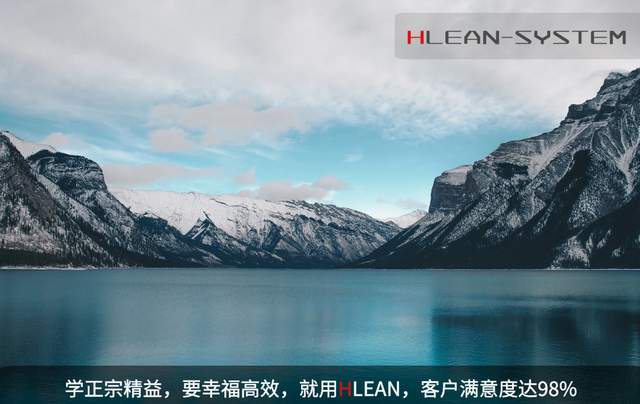
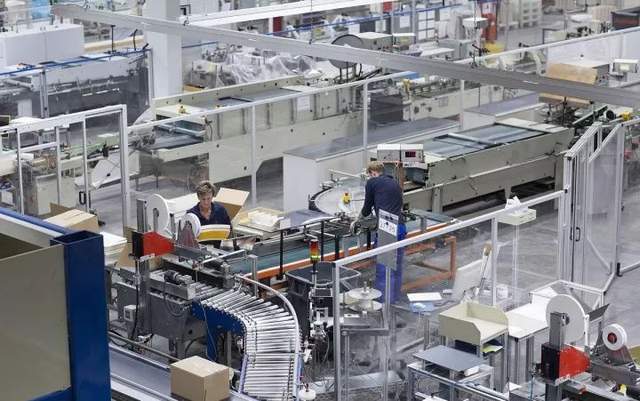
现场案例
某企业某条生产线每月的工作天数为22天,正常工作时间每天为8小时,该生产线做A产品有5个工序,第1个工序(装配1)为28秒,第2个工序(装配2)为34秒,第3个工序(测试)为31秒,第4个工序(总装)为40秒,第4个工序(包装)为24秒),现在客户给了18000个/月的A产品订单,该生产线要如何完成任务?
因为每天完不成819台的任务,该生产线的组长找人事部招了1个新员工,让这个新员工在生产线上5个工序来回帮忙,哪里做不过来就到哪里帮忙做。生产部经理不接受生产线组长这种增加人手的做法,要求进行改善,在不增加人工成本的情况下满足客户的订单需求。
运作思路及具体工作
第一步:明确改善目的和对象
是否因生产量变动(增产或减产)而进行改善;
是否为了提高生产率、减少作业人员;
改善针对某条生产线、某段工序还是整个流程。
第二步:测量对象各工序的时间
秒表法(正常的作业速度,测试20个以上工序时间,取平均值)
第三步:衡量生产线平衡情况
1、生产线平衡率水准
平衡率<85%,水准差,90%>平衡率≥85%,良好;平衡率≥90%,属于优秀
2、客户需求节拍:
生产线瓶颈工时要小于客户需求节拍
A产品平衡率
=生产线各工序时间总和/(瓶颈工时*人员数)
=(28+34+31+40+24)/(40*5)=78.5%
客户需求节拍
=有效出勤时间/[生产计划量*(1+不良率)]
=22*8*3600/18000=35.2秒
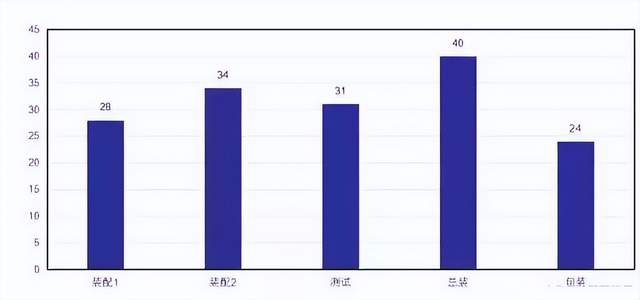
注:瓶颈工时40,客户需求节拍35.2s
第四步:明确增值和非增值时间
增值时间:物料加工、产品组装,质量控制及对产品有利包装。
非增值时间:包括取料距离大于60厘米,弯腰,走动,物料的质量造成的过程返工缺料的等待,停机,工装夹具的维修时间,物料和半成品的运输等。
(非增值时间:指工作中没有能改变产品特性,但目前又是不可获缺的工作,即工序中没有必要或是由于现有设备和工艺无法满足产品质量要求而设置的工作。)
第五步:通过ECRS法则改善平衡
在确保人员和物料正常后,采用ECRS法则改善
案例中ECRS运用
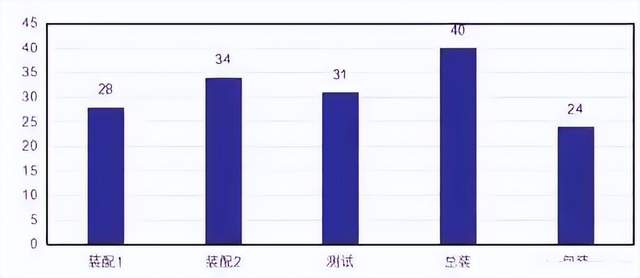
符号 |
名称 |
说明 |
E |
取消Eliminate |
总装中,物料放在员工身后的地上,员工弯腰取料浪费3秒时间。制作物料容器,把物料放在员工左手位置,节约3秒。 |
C |
合并Comebine |
|
R |
重排Rearrange |
1、将装配2的一个3秒的作业动作给装配1做,2个装配的时间都变成了31秒。 2、将总装3秒贴标签动作给包装做,将总装时间再减少3秒,包装时间变为27秒。 |
S |
简化Simplify |
|
第六步:再次衡量生产线平衡情况
改善前
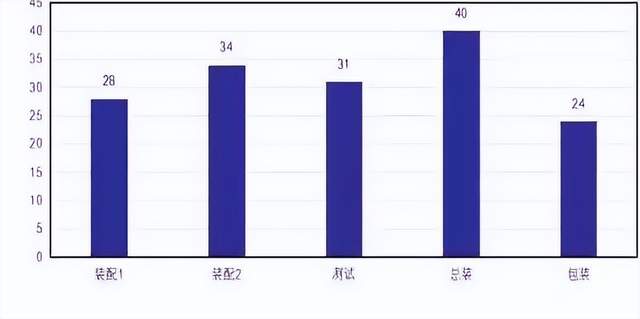
改善后
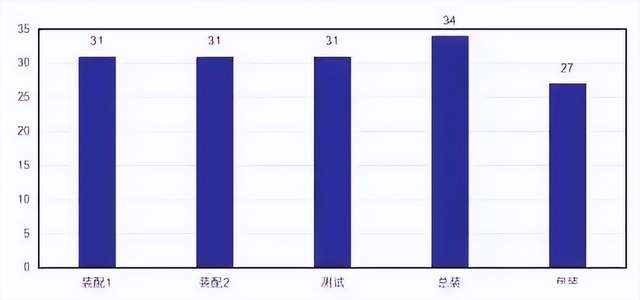
A产品平衡率
=生产线各工序时间总和/(瓶颈工时*人员数)
=(31+31+31+34+27)/(34*5)=90.6%
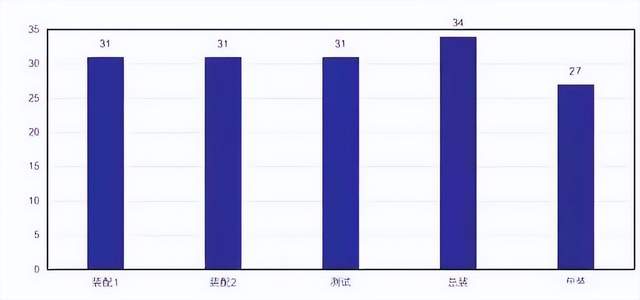
注:瓶颈工时34,客户需求节拍35.2s
第七步:制定改善方案及计划并实施
第八步:PDCA循环改善
成果展示
预装改善前后产线数据对比
项目 |
改善前 |
改善后 |
对比 |
平衡率 |
69.3% |
90.4% |
提高30% |
产能 |
9.23台/小时 |
12.86台/小时 |
提升39% |
总装改善前后产线数据对比
项目 |
改善前 |
改善后 |
对比 |
平衡率 |
66.4% |
86.4% |
提高30% |
产能 |
10.5台/小时 |
12.41台/小时 |
减少1人,产能提升18.2% |
瓶颈工位改善(消除不增值活动)
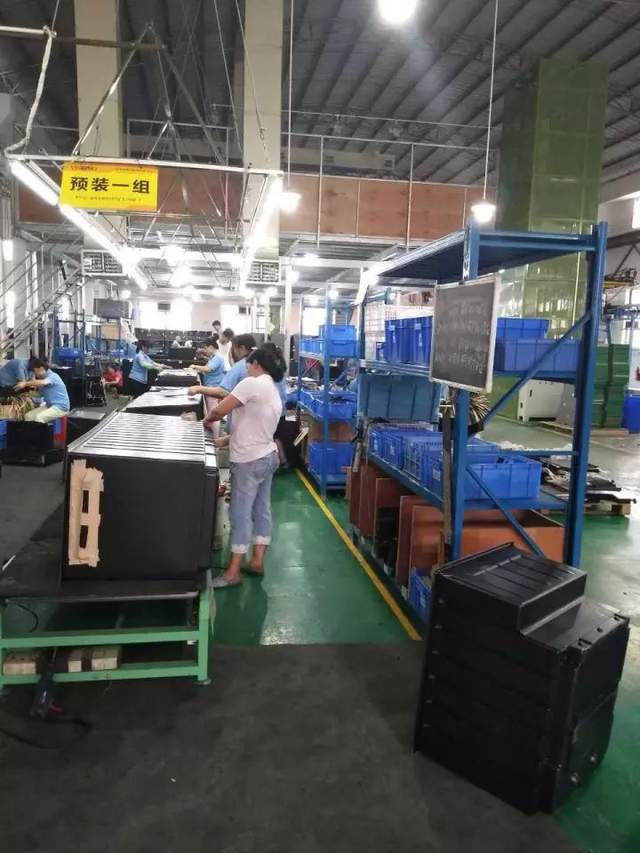
工序2(内胆钻孔、贴内胆胶片),取料走动远浪费工时(工时390秒)
改善前
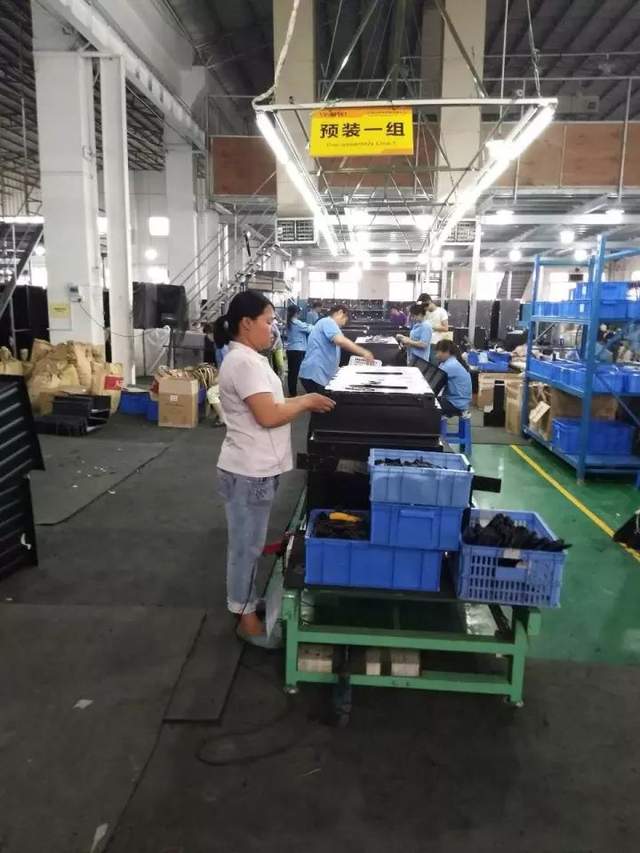
用料盒装料放置工作区旁,减少走动,制作工作架放料盒,工时280秒
改善后
瓶颈工位改善(作业内容调整)
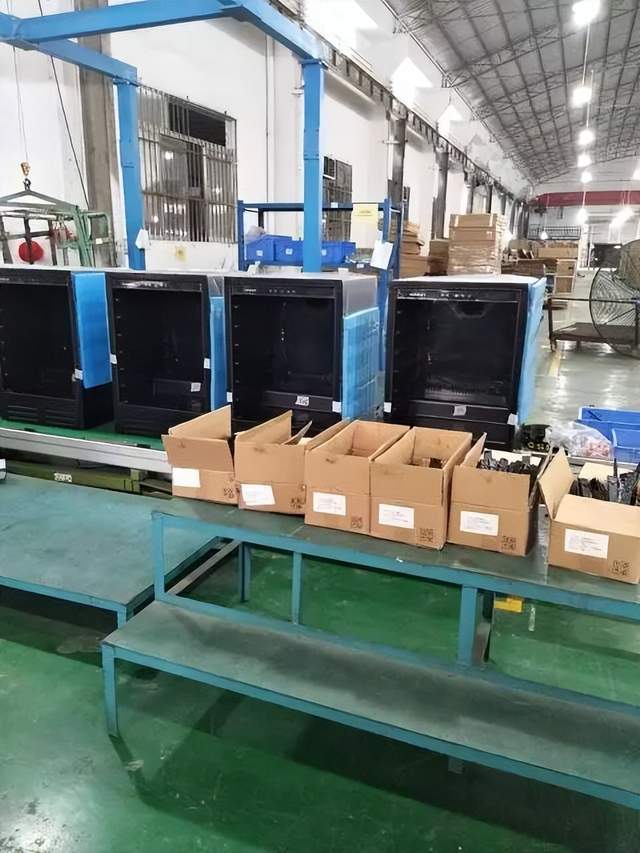
工序1:打导轨(工时343秒/4人),工序瓶颈,其中装导轨作业工时53秒/台
改善前
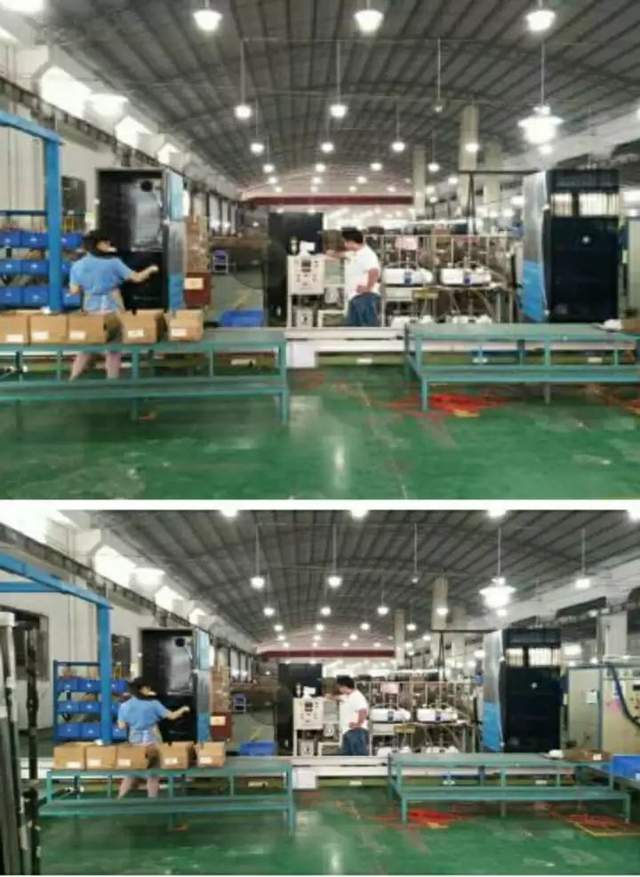
将装导轨作业调整至工序12(装门体),工序12工时由原120秒变为173秒,工序1作业工时减少290秒/台