HLEAN新闻
题记:2016年12月10-16日,中国企业家们带着对精益生产的疑问和疑虑,踏上了寻道之旅。行程间,日本企业扎根制造现场,扎扎实实做企业的经营之道,触动了一众中国企业家们。行程结束已近一个月,回访参团企业家,他们仍对此次日本之行津津乐道,并分享了他们回国后,所做的一些企业方面的举措改变或者自身的一些意识转变,让组织方万分感动,也坚定了广州精弘益立志将传播正宗精益生产思想、技术,帮助制造业提升竞争力,让制造业的人和企业越来越幸福的信念!
丰田从一家生产织布机的企业,华丽转身为世界十大汽车工业公司之一,并成功超越美国车界大佬——美国通用汽车公司和福特汽车公司,更在经历频频发生的召回事件后仍能逆势崛起,创下连续6年位列车辆与零部件行业榜首的光辉业绩。此中起伏转折的故事,一直被各知名企业家津津乐道,而丰田的制胜法宝精益生产方式被极力推崇和效仿。近几年,制造业面临重大的压力,越来越多的中国企业希望通过推行精益生产方式,来应对当前复杂的内外部困境,希望运用精益打造低耗高效的运营模式,转变企业发展方式,实现企业再造升级。然而对于中国企业来说,导入精益并非易事,“专业知识的缺陷”、“思维方式的固化”“业绩管理的缺失”、“强有力企业领导人的缺乏”等问题为中国企业的精益之路设下了重重关卡,阻碍了精益在中国的发展。
鉴于此,精弘益推出《日本精益生产深度考察研修班》,将带领中国企业亲自深入精益生产发源地——名古屋,学习最正宗的,原汁原味的TPS理论,帮助企业管理者走出认识上的误区,同时汲取TPS实践经验,结合企业实际情况,促使丰田生产方式在企业落地及本土化。区别于以往企业定制团学习,本次考察研修班,是公开课形式的,实行小班制教学,学习者均是来自各行各业的老板、总经理、厂长等。
我们带着对精益生产的疑问和疑虑,踏上了寻道之旅。 日本有很多“道”——柔道、花道、茶道,这个道与老子所说的:“道可道,非常道”,一样又不一样。老子所说的“道”,似乎是很玄乎,没有办法一下子学习到的,而日本的“道”,却是真真切切,有迹可循,有章可依,告诉你第一步做什么,第二步做什么,你要做的是如何跟随他们的步骤,一步步去展开工作,就可以找到我们各自的“道”了。
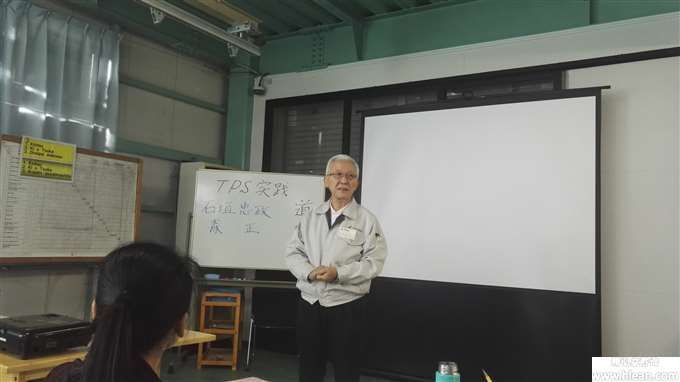
第一站:我们来到 TPS的发源地——日本名古屋 学习原汁原味的精益知识,领略丰田生产方式的两大支柱及构成要素。将在丰田员工岗前技能培训道场内进行实战学习。 担任道场教学的几位老师均在丰田工作40年以上,担任员工培训10年以上。首先,由石垣和森正老师讲解精益生产理论,两大支柱、浪费甄别与动作改善的技巧;其次,讲解作业组合票的填写技巧、生产节拍的计算;再次,通过道场内设有汽车散热器装配生产线,通过模拟生产线上的实际操作,计算生产时间,绘制作业组合票,并通过作业组合票发现生产中的改善点。讲解改善的原则和技巧、导入5个why的工具,提出改善方案,实施改善,并验证改善结果,使学员掌握丰田生产方式的核心,标准作业与作业改善的精髓。最后,讲解改善后,生产效率提升,省出来的人力,如何来调配和运用。
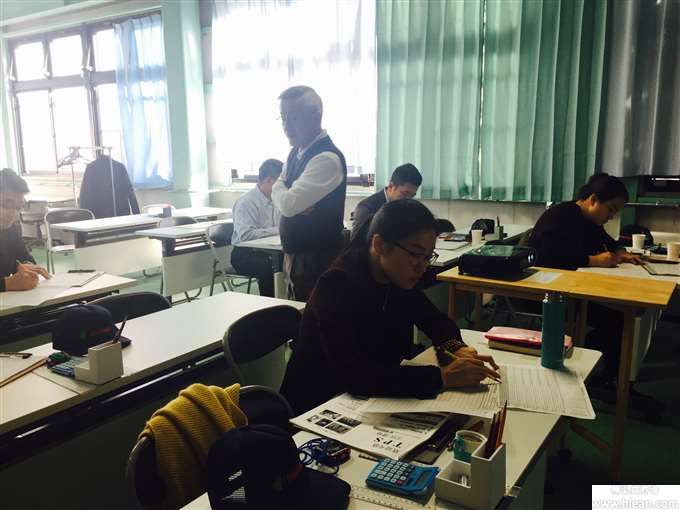
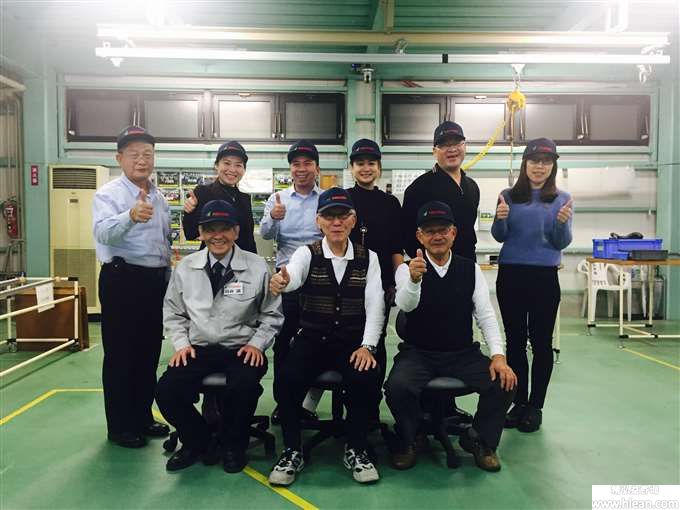
上课期间,石垣老师提出了:一秒一步一円(元),都不可以浪费的理念。他拿出一个拆封过的信封说,在丰田,这样的信封被贴上一些标签纸后,会被循环利用。作为丰田这样的大公司,在信封这么小的日常用品上,都如此注重成本概念,让来学习的企业家们感触良深。
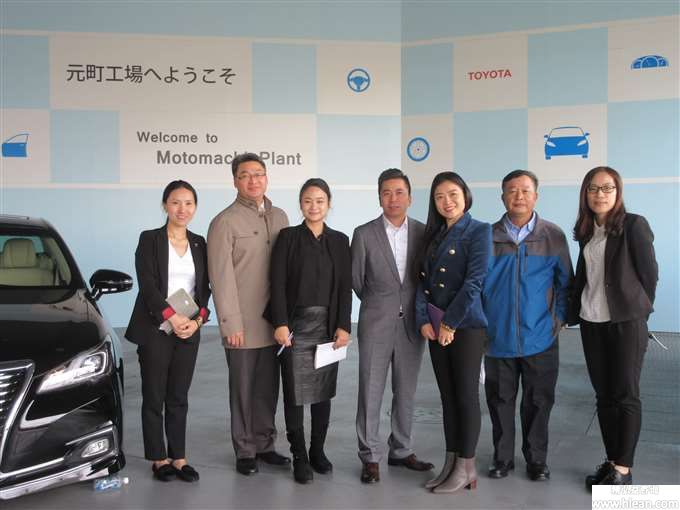
第二站:丰田生产基地——元町工厂。丰田公司有一个重要理念叫“现地现物”,不到丰田公司生产现场,难以把握丰田精益生产方式的精髓,难以领会丰田精益生产方式的真谛。元町厂是丰田精益生产的发源地,也是丰田皇冠车的主要产地,从1959成立至今,已出产了第13代皇冠。在元町厂,您可以看到原汁原味的“看板管理”和“准时生产”的运用,目睹“拉绳呼叫开关”(即安灯系统)的管理奇妙。元町工厂建成近60年,但一点都不显得老旧,充满活力,偌大的厂房内,流水线舒缓地流动,新老设备同时运行,零部件通过叉车、无人车和运输通道三管齐下有序地配给,现场员工自动地工作,人机一体,浑然天成,一股敬意禁不住在心中油然而生。
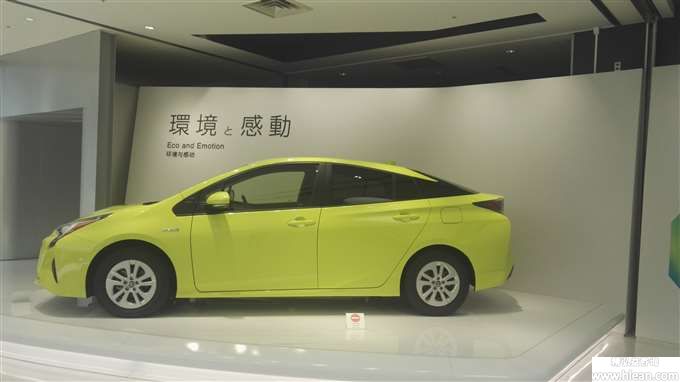
接着来到同样位于元町的丰田会馆继续参观。丰田会馆里展示着丰田公司的产品和技术,更展示着丰田公司掩藏在产品背后的价值理念。譬如:丰田人从事的是丰富人们生活的事业;丰田公司不仅仅是制造精美车辆,更要为地球和社会可持续发展做贡献;制造即育人;带“人”字旁的“自働化”与“准时生产”是“丰田生产方式”的两大支柱等理念。
下午是由丰田制造信息系统建设者,持续可能型制造与人才培养协会会长 – 黑岩惠老师为学员们讲解IOT的应用。物联网、车联网、工业4.0、智能化生产众说纷纭。在我们还在讨论如何规避人口红利下降,以及如何应对招工难,员工流失率高等问题的时候,某些先进企业已经在帮机器人开新员工欢迎大会了。国情、企业实际情况的不同,差距很大。虽然IOT在各行各业有很多应用,但高新技术,同时代表着高昂的成本投入,如何选择和平衡智能化生产和手工作业间的关系?黑岩惠老师会逐一分享。
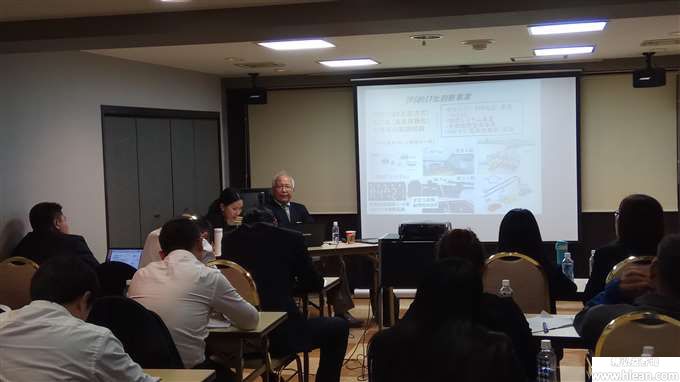
丰田之行后,有位学员分享到:坚持“以人为本”的自动化理念,让人自动自发工作,才是“丰田生产方式”的精髓!
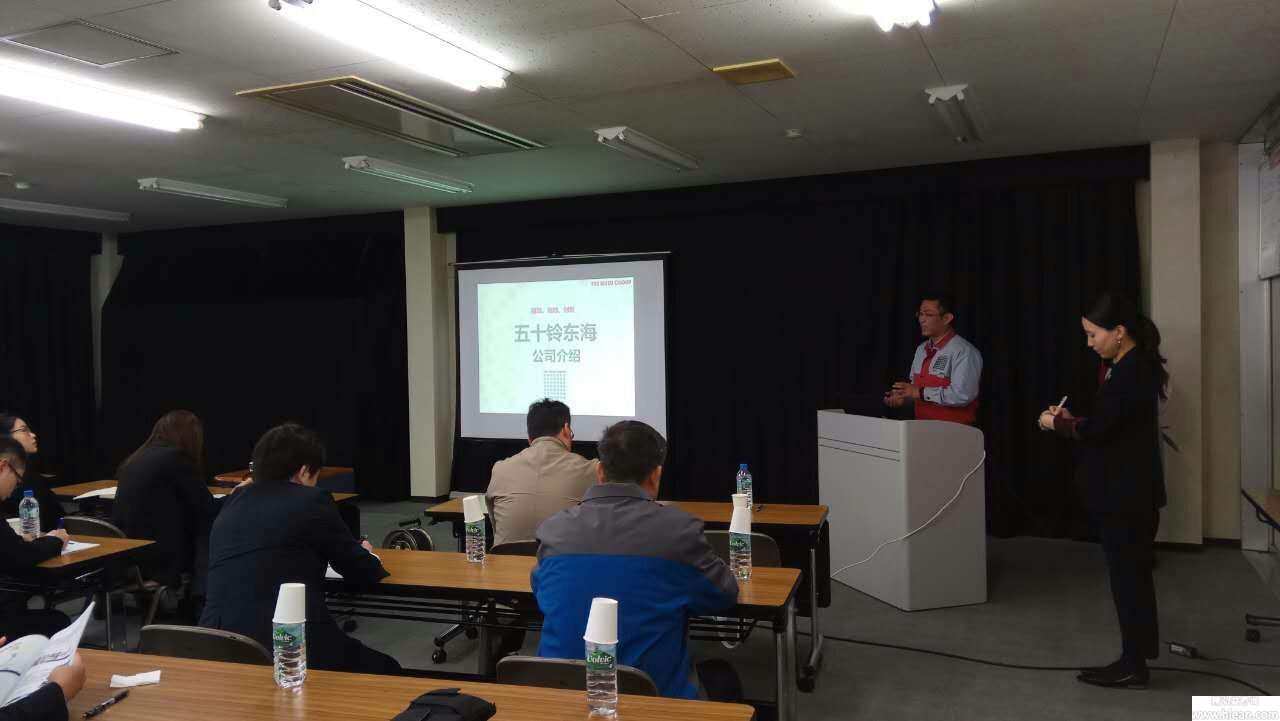
第三站:五十铃东海服务中心
五十铃是世界上最具规模及历史最悠久的商用汽车制造企业之一,其致力于应用一流的技术和工艺,开发高科技、高可靠性、节油环保的汽车及发动机产品,向世界各地的用户提供高效率的运输工具,共同创造美好未来。五十铃东海服务中心,主要的业务是钢板制造。五十铃一直秉持着公司创始人“成为社会中不可取代的存在”的理念,以及"最大限度发挥个人及组织优势"的精神,孕育出了独特管理技术,和在日常的实践中完善的各种机制。
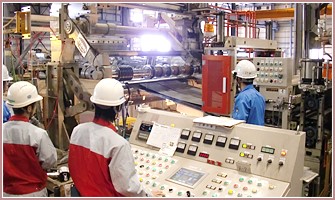
五十铃负责人为我们详细介绍了五十铃集团的主干业务系统ATOM。采用此系统后,实现了"公司内部生产周期缩短50%"、"总成本削减50%"、"处理能力提高50%"等指标。也分享了其通过员工智慧以及团体作战优势,对工厂整体布局进行改善的案例。
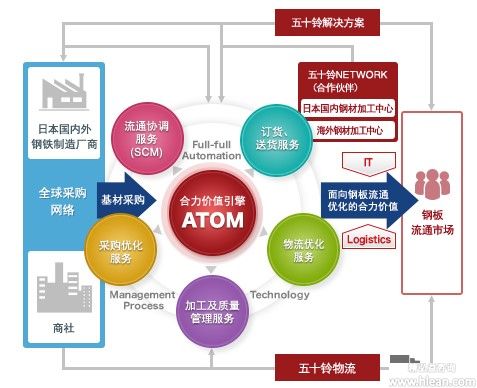
在员工餐厅,您能看到各类生产看板,员工改善成果展示、生产计划、达成率、故障率、客户投诉率、节能降耗率,各部门年度指标均能在这里找到,而这些数据都是及时更新,在实际运行的,而不是为了应对外来参观而设。
在生产现场里,您还能看到几排小书柜,里面有生产相关的书籍和一些生产数据的记录资料,这是他们技能培训和品质检查培训的基地。公司内部是没有品质部门的,全员参与到各个环节的品质检测,而如何推行这种机制,如何培养多能工,厂长将一一为大家解答。
第四站:村田机械 创立于1935年,是日本具有代表性的机械厂商。从发明空气捻接器以来,以占有世界第一市场分额的自动络筒机等纤维机械为首,先后广泛涉入了机床、信息设备、物流设备、面向液晶工厂/半导体工厂的自动化设备等领域。在日本国内拥有6个生产基地,4个技术中心,6000余名员工。村田机械实施生产革新已有近20年的历史。 1996年作为日本最早一批改善推进企业,在大分工厂导入单元生产。随后在车床机械,物流设备,定制非标的大型机械制造也全部改为单元生产。与此同时,以单元生产方式为基础,在活用现场每一位员工的创造性的同时,通过采用“一台流”的生产方式来对应需求变化,实施变种变量的混流生产及单元生产,结合产品特性,市场特性选择生产方式。
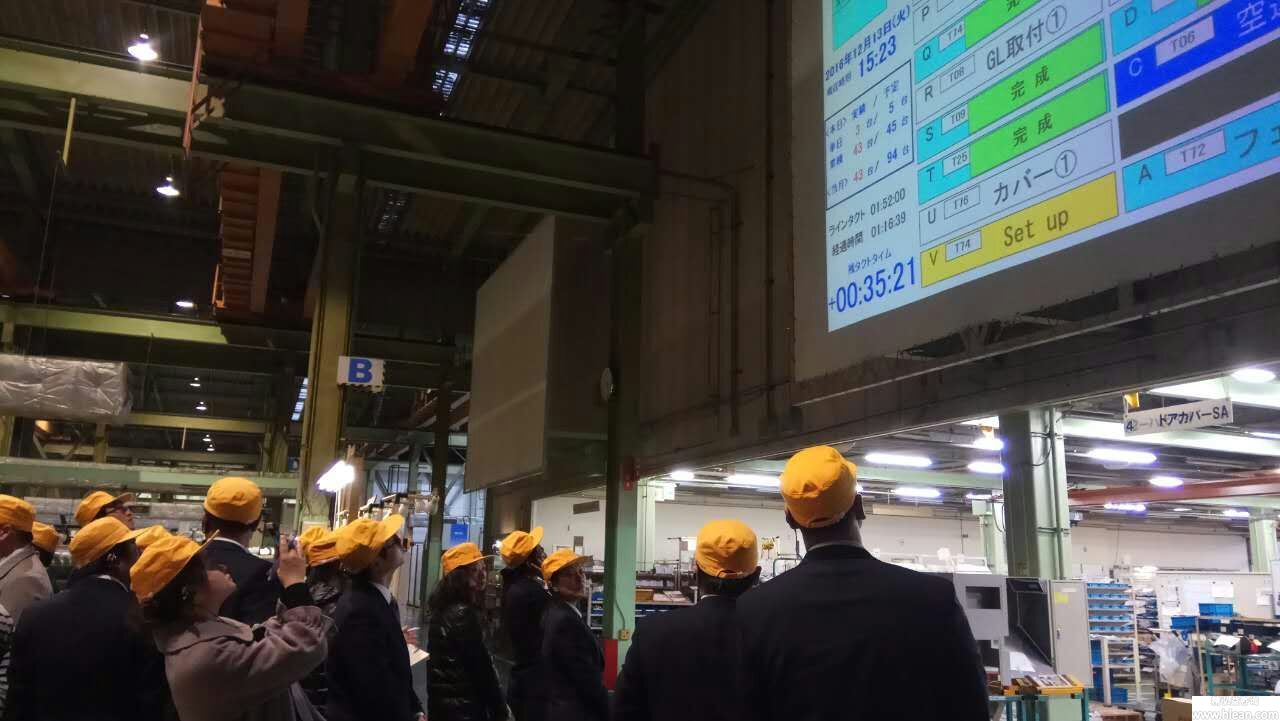
村田机械在可视化应用、看板管理和多能工培养方面做得很好。在生产现场,大家可以看到“一台流”的运作情况,现场悬挂的电视墙能实时看到生产进度,以及22个生产小组的工作状态和工作位置。22个小组的生产人员人手一部平板电脑,到工位后,通过系统调出对应设备的生产工单,根据工单指示进行生产,而工单上会注明该工序所需的时间。
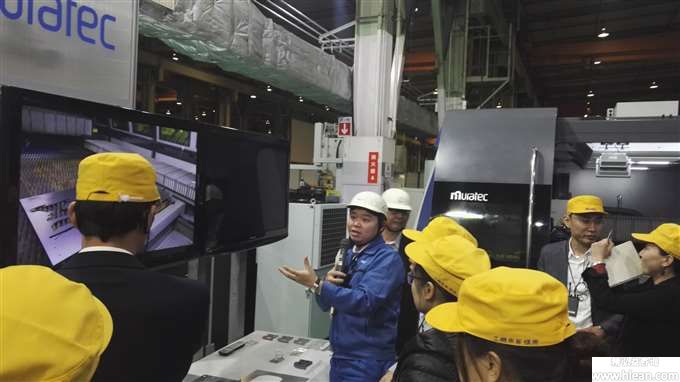
“一台流”的背后,有一个庞大而细致的信息化系统在支撑。从客户提出需求开始,售前支持将每台设备所需要的功能和要求通过系统传达到研发部。研发部门会根据客户需求,对每台机器进行设计,并确定所需的工序和零部件。系统中有每一个工序和零部件安装所需的工时,所以一旦工序和零部件勾选确认后,整台机器的制造成本和所需工时就能马上计算出来。
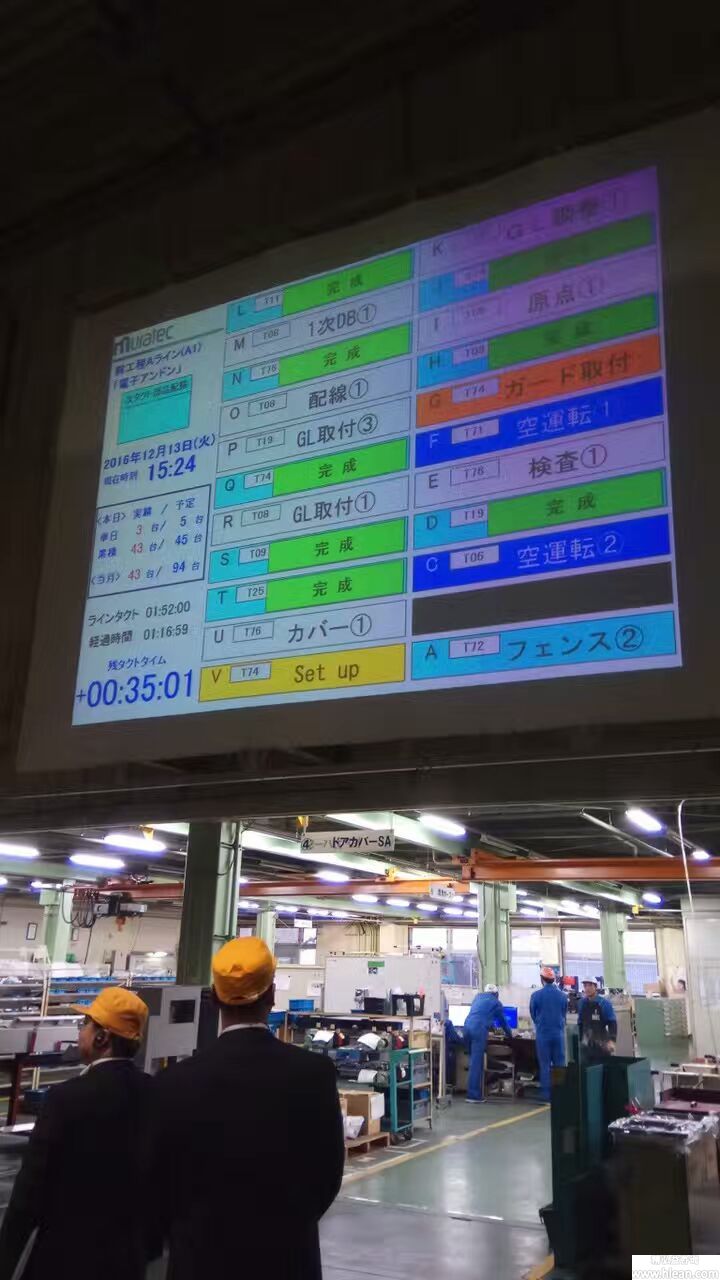
在仓库管理方面,村田机械也有独到之处。仓管区由横纵线分成了大小统一的方格子,在仓管区会有一个电视墙,您可以透过显示器看到每一个区域摆放的是什么物资,哪些区域是空闲的,一目了然。
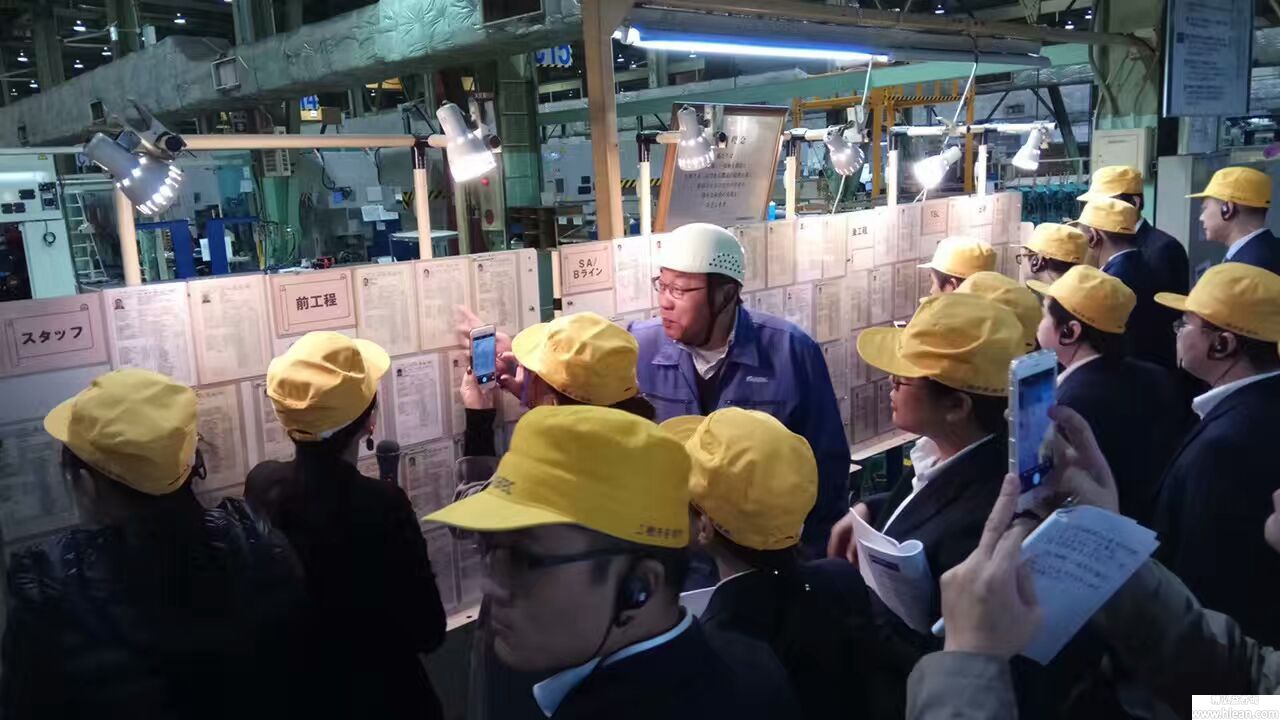
生产现场还有一排看板墙,展示了大分工厂240多名员工,每一个员工的技能模型图,内部也有一系列的制度和措施来支撑多能工的养成。在现场还有一个很有意思的现象。据我们当天所接触的员工来看,起码有4个国籍的员工——日本、中国、印度、欧洲,大家都有条不紊地遵循着各种规章制度。如何让不同国籍不同文化背景的人,接受同一套管理模式,背后肯定有很多故事。
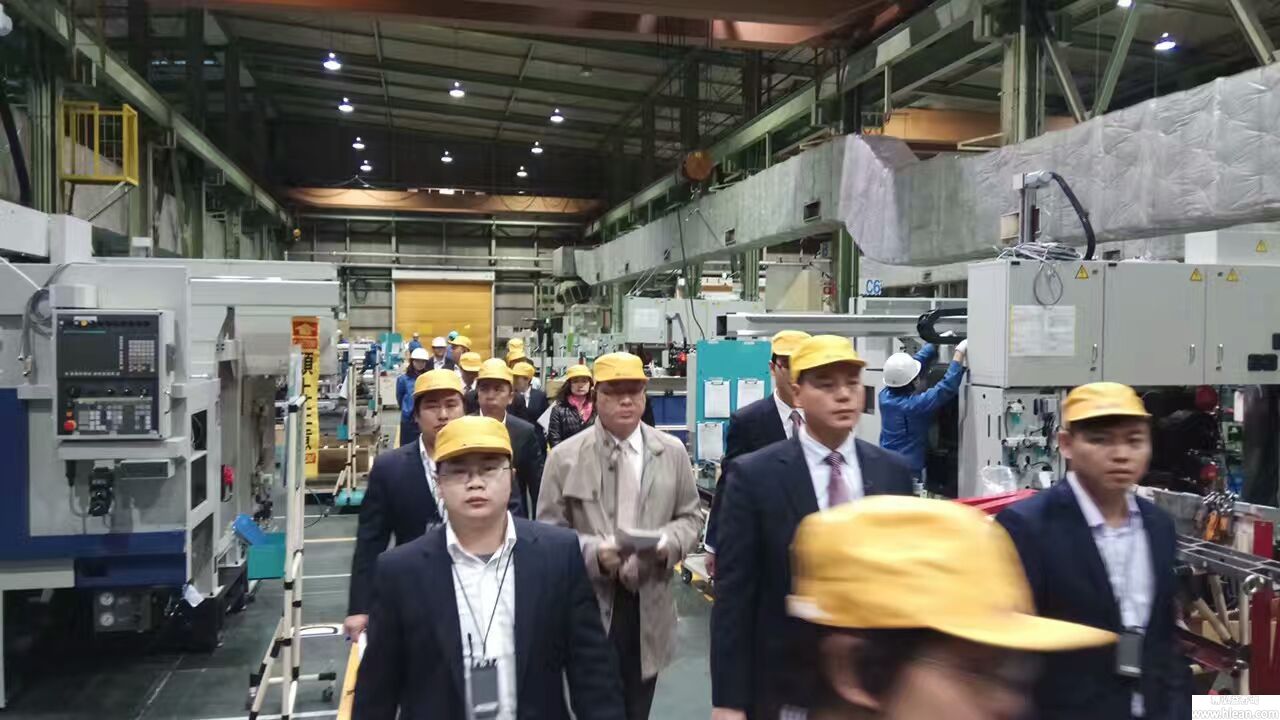
第五站:大福物流
世界最大的物流系统综合制造厂家,智能物流的幕后英雄。创建与1937年,最早生产气锤,锻压加工机,随着日本经济的复兴与发展,开始涉足物料的运输及管理物流。。从60年代起开始生产立体自动仓库和自动化无人搬送车。2006年度株式会社大福集团的营业额超过2000亿日元,在全球拥有40多个分支机构和约5000名的社员,位于风景秀丽的琵琶湖畔群山环保中的滋贺生产基地占地面积120万平方米(2000亩),11个现代化厂房建筑群与优美的自然环境和谐相处。
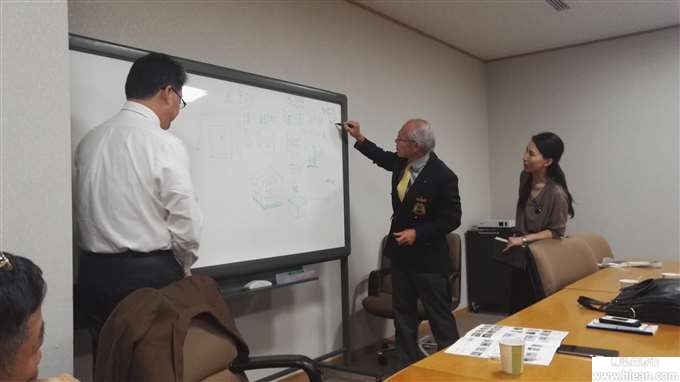
在“日新馆”,馆长为我们展示了立体自动仓库的工作情况,有输送系统 、存储系统 、分拣和拣选系统 、控制系统 、物流设备,在这里能看到目前世界上最快速的输送设备,也能看到智能物流在各个行业应用的案例展示。其中最让学员们惊叹的莫过于智能物流在骨灰盒保管方面的应用了。你也可以带着问题,与馆长讨论贵公司物流系统,让他为贵司的物流系统改进出谋划策。
第六站:大和房屋
大和房屋集团的核心企业大和房屋工业株式会社成立于1955年,是日本最大的,也是最早实现住宅工业化的企业。本次将参观大和房屋的核心生产工厂-奈良工厂。 奈良工厂是制造业未来智能环保工厂的样板工厂。2013年12月投产使用,主要生产公司的主力产品“钢骨类住宅”,钢骨类住宅的主要构造均使用钢骨,为了保证高品质,同时为了保证强度,提升耐力度,在焊接方面下了很多功夫。 耐力钢构件焊接选择人工焊接,非耐力件的焊接由机器人完成。生产现场工业用机器人和熟练技术人员相互协助,实现完美结合。
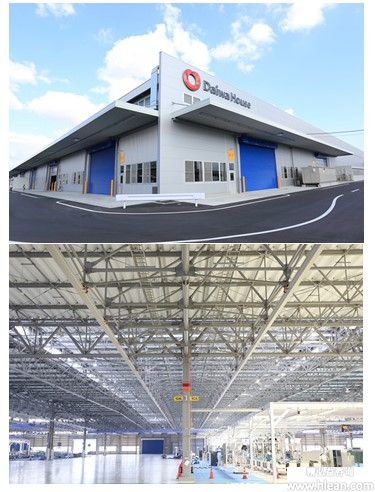
在制造现场,随处可见现场管理的信息化,生产进度信息,抬头即可见。因为房屋生产有很多非标件,所以整个生产过程,每一个产品都有一一对应的配件系统,予以配件。
负责人谷久先生给大家展示智能环保型工厂的设计理念,从充分利用自然光资源,减少室内照明;充分利用自然通风设备关闭,来调节室内温度,进而减少空调、风扇或者制暖设备的用电量;展示了无动力设置的关闭门等环保型设施;利用屋顶的特殊设计,收集太阳能,达到储备电能的设计。在这里没有粉尘、没有噪音,没有工业有毒气体,一切都在绿色环保的标准下进行。在一片祥和的奈良,我们结束了本次研修学习。
7天6夜的行程虽然早已结束,但给企业家们留下的触动却支持着他们在制造业之路上越走越远,越走越矫健!
丰田从一家生产织布机的企业,华丽转身为世界十大汽车工业公司之一,并成功超越美国车界大佬——美国通用汽车公司和福特汽车公司,更在经历频频发生的召回事件后仍能逆势崛起,创下连续6年位列车辆与零部件行业榜首的光辉业绩。此中起伏转折的故事,一直被各知名企业家津津乐道,而丰田的制胜法宝精益生产方式被极力推崇和效仿。近几年,制造业面临重大的压力,越来越多的中国企业希望通过推行精益生产方式,来应对当前复杂的内外部困境,希望运用精益打造低耗高效的运营模式,转变企业发展方式,实现企业再造升级。然而对于中国企业来说,导入精益并非易事,“专业知识的缺陷”、“思维方式的固化”“业绩管理的缺失”、“强有力企业领导人的缺乏”等问题为中国企业的精益之路设下了重重关卡,阻碍了精益在中国的发展。
鉴于此,精弘益推出《日本精益生产深度考察研修班》,将带领中国企业亲自深入精益生产发源地——名古屋,学习最正宗的,原汁原味的TPS理论,帮助企业管理者走出认识上的误区,同时汲取TPS实践经验,结合企业实际情况,促使丰田生产方式在企业落地及本土化。区别于以往企业定制团学习,本次考察研修班,是公开课形式的,实行小班制教学,学习者均是来自各行各业的老板、总经理、厂长等。
我们带着对精益生产的疑问和疑虑,踏上了寻道之旅。 日本有很多“道”——柔道、花道、茶道,这个道与老子所说的:“道可道,非常道”,一样又不一样。老子所说的“道”,似乎是很玄乎,没有办法一下子学习到的,而日本的“道”,却是真真切切,有迹可循,有章可依,告诉你第一步做什么,第二步做什么,你要做的是如何跟随他们的步骤,一步步去展开工作,就可以找到我们各自的“道”了。
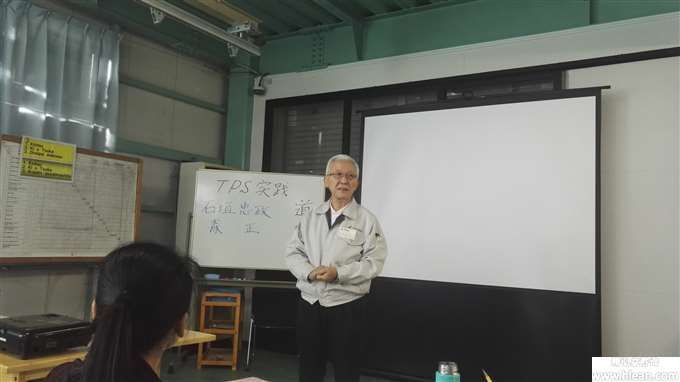
第一站:我们来到 TPS的发源地——日本名古屋 学习原汁原味的精益知识,领略丰田生产方式的两大支柱及构成要素。将在丰田员工岗前技能培训道场内进行实战学习。 担任道场教学的几位老师均在丰田工作40年以上,担任员工培训10年以上。首先,由石垣和森正老师讲解精益生产理论,两大支柱、浪费甄别与动作改善的技巧;其次,讲解作业组合票的填写技巧、生产节拍的计算;再次,通过道场内设有汽车散热器装配生产线,通过模拟生产线上的实际操作,计算生产时间,绘制作业组合票,并通过作业组合票发现生产中的改善点。讲解改善的原则和技巧、导入5个why的工具,提出改善方案,实施改善,并验证改善结果,使学员掌握丰田生产方式的核心,标准作业与作业改善的精髓。最后,讲解改善后,生产效率提升,省出来的人力,如何来调配和运用。
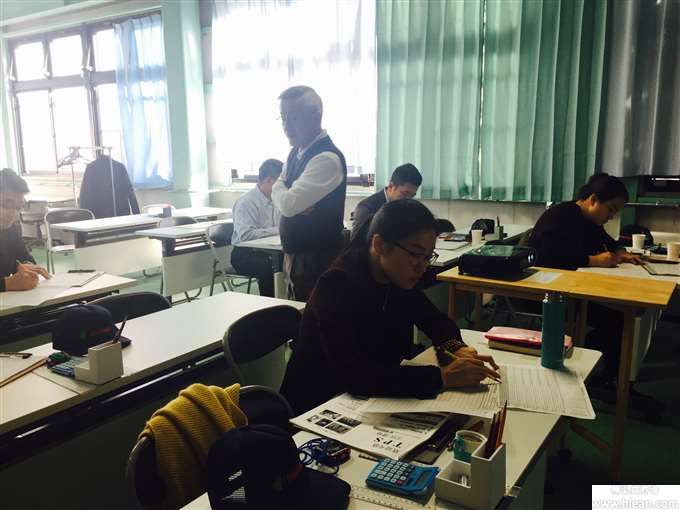
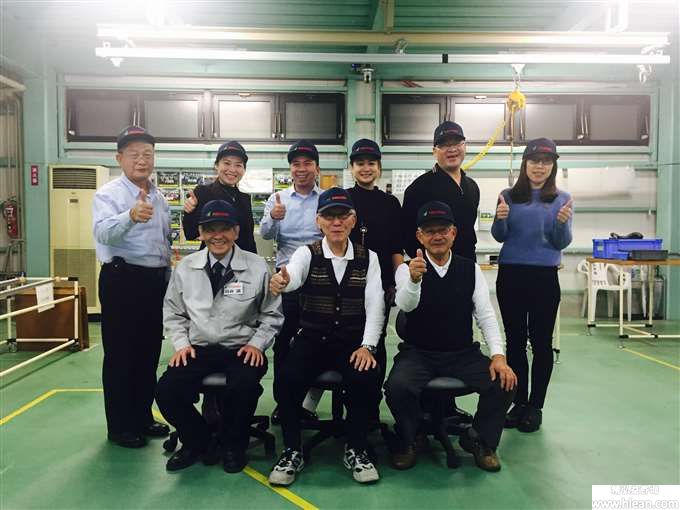
上课期间,石垣老师提出了:一秒一步一円(元),都不可以浪费的理念。他拿出一个拆封过的信封说,在丰田,这样的信封被贴上一些标签纸后,会被循环利用。作为丰田这样的大公司,在信封这么小的日常用品上,都如此注重成本概念,让来学习的企业家们感触良深。
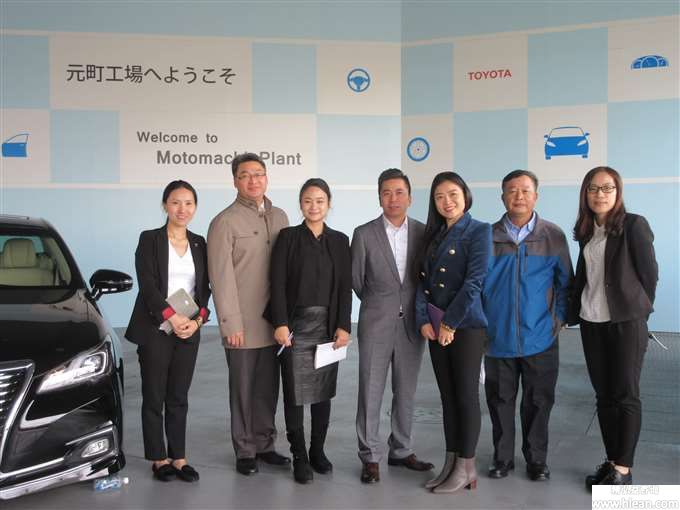
第二站:丰田生产基地——元町工厂。丰田公司有一个重要理念叫“现地现物”,不到丰田公司生产现场,难以把握丰田精益生产方式的精髓,难以领会丰田精益生产方式的真谛。元町厂是丰田精益生产的发源地,也是丰田皇冠车的主要产地,从1959成立至今,已出产了第13代皇冠。在元町厂,您可以看到原汁原味的“看板管理”和“准时生产”的运用,目睹“拉绳呼叫开关”(即安灯系统)的管理奇妙。元町工厂建成近60年,但一点都不显得老旧,充满活力,偌大的厂房内,流水线舒缓地流动,新老设备同时运行,零部件通过叉车、无人车和运输通道三管齐下有序地配给,现场员工自动地工作,人机一体,浑然天成,一股敬意禁不住在心中油然而生。
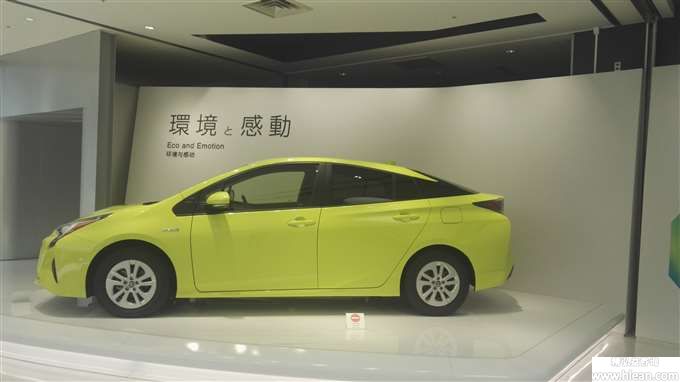
接着来到同样位于元町的丰田会馆继续参观。丰田会馆里展示着丰田公司的产品和技术,更展示着丰田公司掩藏在产品背后的价值理念。譬如:丰田人从事的是丰富人们生活的事业;丰田公司不仅仅是制造精美车辆,更要为地球和社会可持续发展做贡献;制造即育人;带“人”字旁的“自働化”与“准时生产”是“丰田生产方式”的两大支柱等理念。
下午是由丰田制造信息系统建设者,持续可能型制造与人才培养协会会长 – 黑岩惠老师为学员们讲解IOT的应用。物联网、车联网、工业4.0、智能化生产众说纷纭。在我们还在讨论如何规避人口红利下降,以及如何应对招工难,员工流失率高等问题的时候,某些先进企业已经在帮机器人开新员工欢迎大会了。国情、企业实际情况的不同,差距很大。虽然IOT在各行各业有很多应用,但高新技术,同时代表着高昂的成本投入,如何选择和平衡智能化生产和手工作业间的关系?黑岩惠老师会逐一分享。
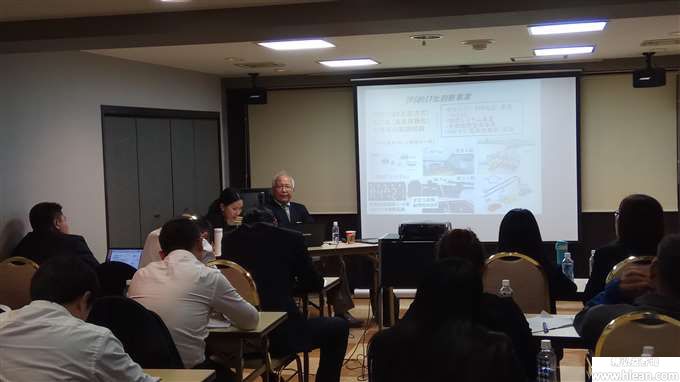
丰田之行后,有位学员分享到:坚持“以人为本”的自动化理念,让人自动自发工作,才是“丰田生产方式”的精髓!
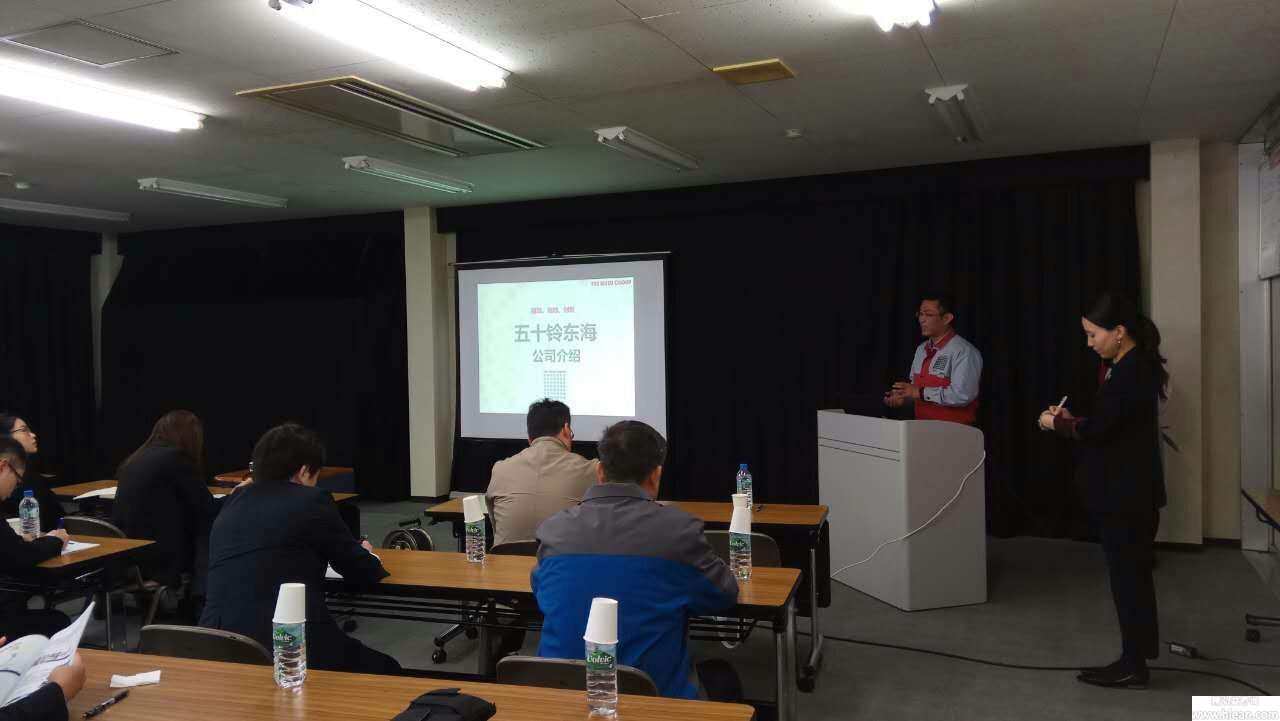
第三站:五十铃东海服务中心
五十铃是世界上最具规模及历史最悠久的商用汽车制造企业之一,其致力于应用一流的技术和工艺,开发高科技、高可靠性、节油环保的汽车及发动机产品,向世界各地的用户提供高效率的运输工具,共同创造美好未来。五十铃东海服务中心,主要的业务是钢板制造。五十铃一直秉持着公司创始人“成为社会中不可取代的存在”的理念,以及"最大限度发挥个人及组织优势"的精神,孕育出了独特管理技术,和在日常的实践中完善的各种机制。
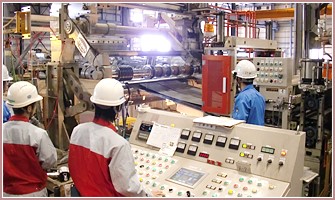
五十铃负责人为我们详细介绍了五十铃集团的主干业务系统ATOM。采用此系统后,实现了"公司内部生产周期缩短50%"、"总成本削减50%"、"处理能力提高50%"等指标。也分享了其通过员工智慧以及团体作战优势,对工厂整体布局进行改善的案例。
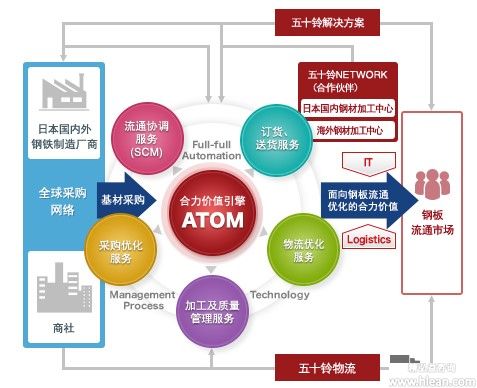
在员工餐厅,您能看到各类生产看板,员工改善成果展示、生产计划、达成率、故障率、客户投诉率、节能降耗率,各部门年度指标均能在这里找到,而这些数据都是及时更新,在实际运行的,而不是为了应对外来参观而设。
在生产现场里,您还能看到几排小书柜,里面有生产相关的书籍和一些生产数据的记录资料,这是他们技能培训和品质检查培训的基地。公司内部是没有品质部门的,全员参与到各个环节的品质检测,而如何推行这种机制,如何培养多能工,厂长将一一为大家解答。
第四站:村田机械 创立于1935年,是日本具有代表性的机械厂商。从发明空气捻接器以来,以占有世界第一市场分额的自动络筒机等纤维机械为首,先后广泛涉入了机床、信息设备、物流设备、面向液晶工厂/半导体工厂的自动化设备等领域。在日本国内拥有6个生产基地,4个技术中心,6000余名员工。村田机械实施生产革新已有近20年的历史。 1996年作为日本最早一批改善推进企业,在大分工厂导入单元生产。随后在车床机械,物流设备,定制非标的大型机械制造也全部改为单元生产。与此同时,以单元生产方式为基础,在活用现场每一位员工的创造性的同时,通过采用“一台流”的生产方式来对应需求变化,实施变种变量的混流生产及单元生产,结合产品特性,市场特性选择生产方式。
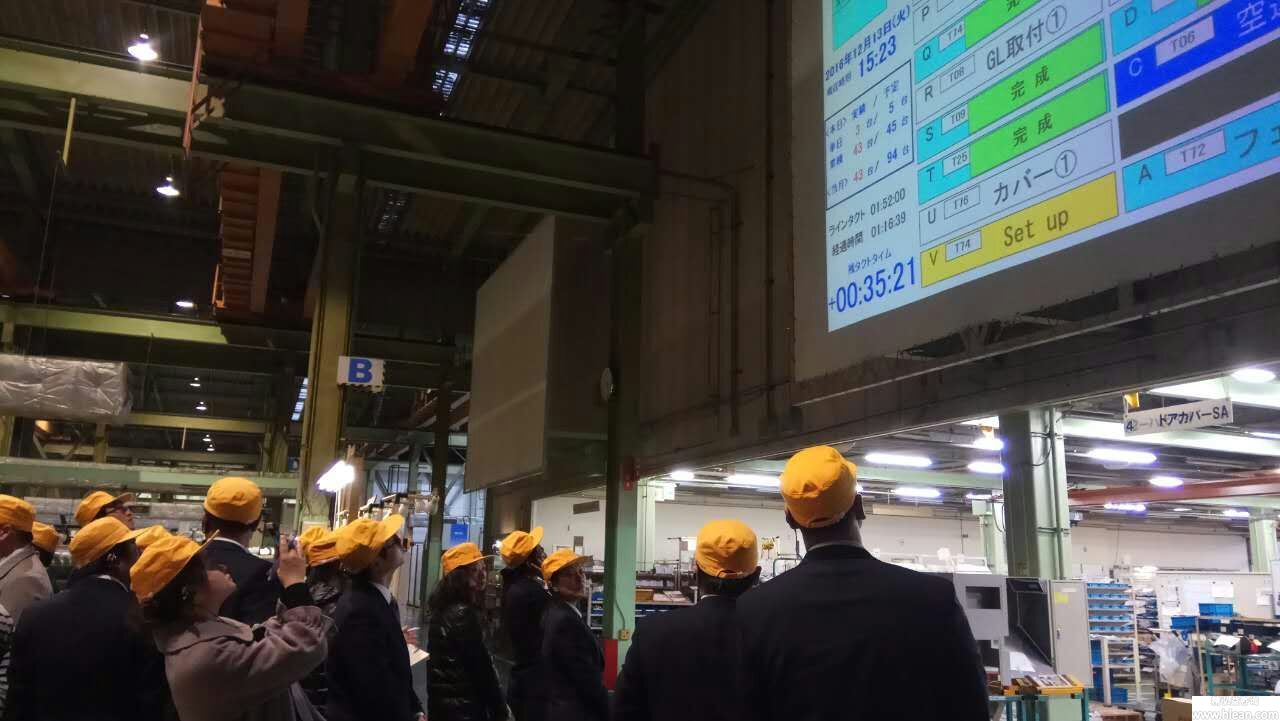
村田机械在可视化应用、看板管理和多能工培养方面做得很好。在生产现场,大家可以看到“一台流”的运作情况,现场悬挂的电视墙能实时看到生产进度,以及22个生产小组的工作状态和工作位置。22个小组的生产人员人手一部平板电脑,到工位后,通过系统调出对应设备的生产工单,根据工单指示进行生产,而工单上会注明该工序所需的时间。
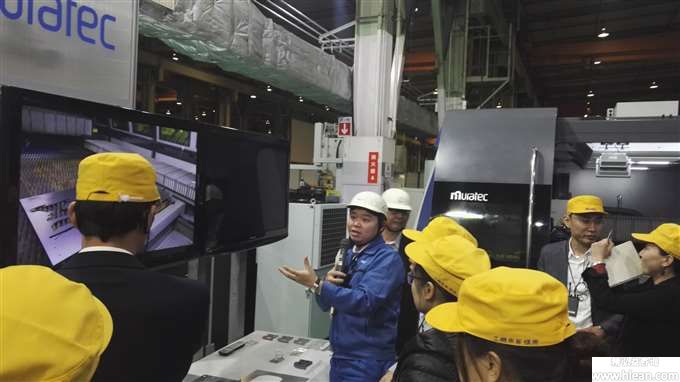
“一台流”的背后,有一个庞大而细致的信息化系统在支撑。从客户提出需求开始,售前支持将每台设备所需要的功能和要求通过系统传达到研发部。研发部门会根据客户需求,对每台机器进行设计,并确定所需的工序和零部件。系统中有每一个工序和零部件安装所需的工时,所以一旦工序和零部件勾选确认后,整台机器的制造成本和所需工时就能马上计算出来。
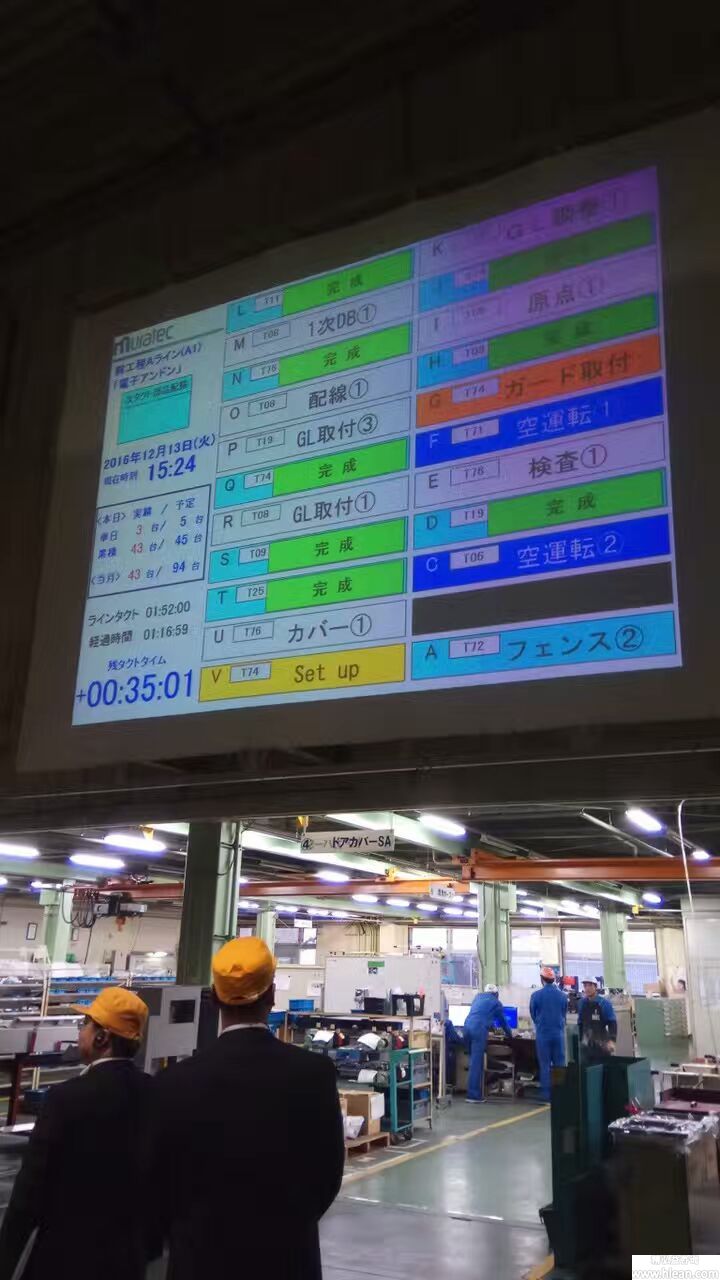
在仓库管理方面,村田机械也有独到之处。仓管区由横纵线分成了大小统一的方格子,在仓管区会有一个电视墙,您可以透过显示器看到每一个区域摆放的是什么物资,哪些区域是空闲的,一目了然。
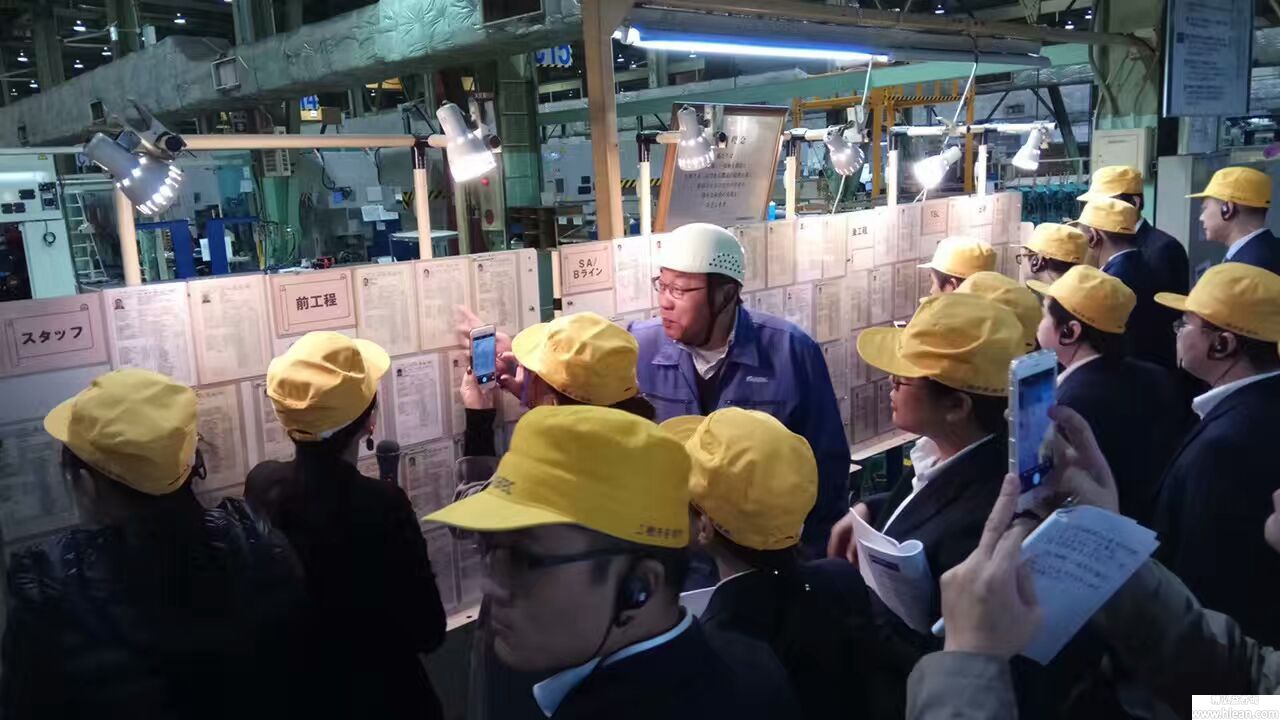
生产现场还有一排看板墙,展示了大分工厂240多名员工,每一个员工的技能模型图,内部也有一系列的制度和措施来支撑多能工的养成。在现场还有一个很有意思的现象。据我们当天所接触的员工来看,起码有4个国籍的员工——日本、中国、印度、欧洲,大家都有条不紊地遵循着各种规章制度。如何让不同国籍不同文化背景的人,接受同一套管理模式,背后肯定有很多故事。
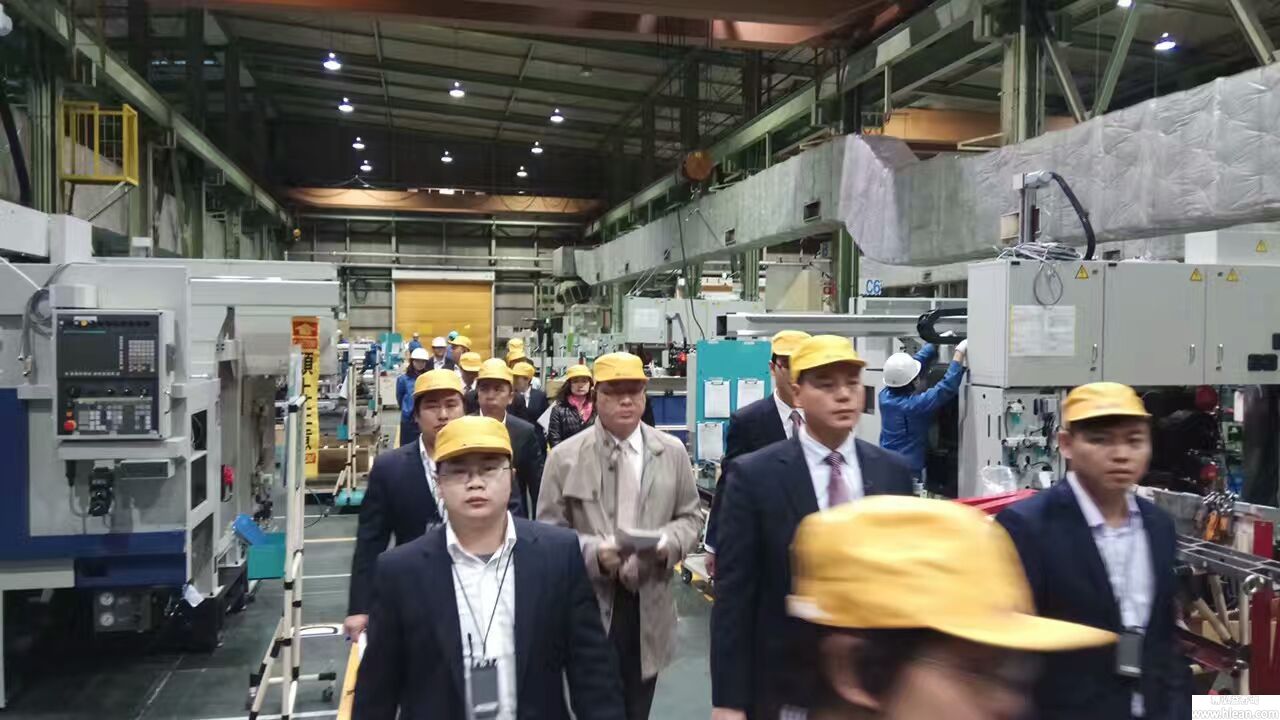
第五站:大福物流
世界最大的物流系统综合制造厂家,智能物流的幕后英雄。创建与1937年,最早生产气锤,锻压加工机,随着日本经济的复兴与发展,开始涉足物料的运输及管理物流。。从60年代起开始生产立体自动仓库和自动化无人搬送车。2006年度株式会社大福集团的营业额超过2000亿日元,在全球拥有40多个分支机构和约5000名的社员,位于风景秀丽的琵琶湖畔群山环保中的滋贺生产基地占地面积120万平方米(2000亩),11个现代化厂房建筑群与优美的自然环境和谐相处。
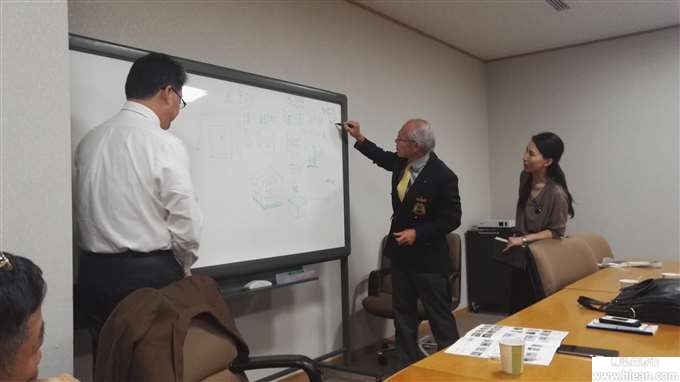
在“日新馆”,馆长为我们展示了立体自动仓库的工作情况,有输送系统 、存储系统 、分拣和拣选系统 、控制系统 、物流设备,在这里能看到目前世界上最快速的输送设备,也能看到智能物流在各个行业应用的案例展示。其中最让学员们惊叹的莫过于智能物流在骨灰盒保管方面的应用了。你也可以带着问题,与馆长讨论贵公司物流系统,让他为贵司的物流系统改进出谋划策。
第六站:大和房屋
大和房屋集团的核心企业大和房屋工业株式会社成立于1955年,是日本最大的,也是最早实现住宅工业化的企业。本次将参观大和房屋的核心生产工厂-奈良工厂。 奈良工厂是制造业未来智能环保工厂的样板工厂。2013年12月投产使用,主要生产公司的主力产品“钢骨类住宅”,钢骨类住宅的主要构造均使用钢骨,为了保证高品质,同时为了保证强度,提升耐力度,在焊接方面下了很多功夫。 耐力钢构件焊接选择人工焊接,非耐力件的焊接由机器人完成。生产现场工业用机器人和熟练技术人员相互协助,实现完美结合。
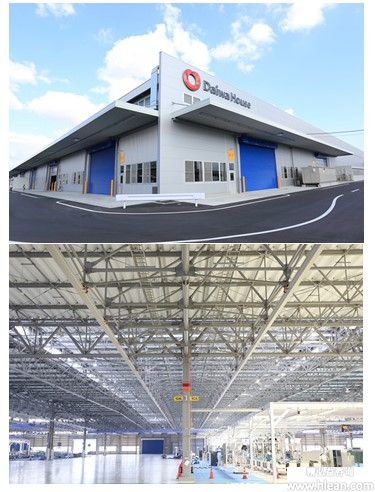
在制造现场,随处可见现场管理的信息化,生产进度信息,抬头即可见。因为房屋生产有很多非标件,所以整个生产过程,每一个产品都有一一对应的配件系统,予以配件。
负责人谷久先生给大家展示智能环保型工厂的设计理念,从充分利用自然光资源,减少室内照明;充分利用自然通风设备关闭,来调节室内温度,进而减少空调、风扇或者制暖设备的用电量;展示了无动力设置的关闭门等环保型设施;利用屋顶的特殊设计,收集太阳能,达到储备电能的设计。在这里没有粉尘、没有噪音,没有工业有毒气体,一切都在绿色环保的标准下进行。在一片祥和的奈良,我们结束了本次研修学习。
7天6夜的行程虽然早已结束,但给企业家们留下的触动却支持着他们在制造业之路上越走越远,越走越矫健!