电子期刊
3.现场改善的推进方法
3-3.改善时的注意点
3-3-1.改善时对质量问题的认识
作为生产性企业,向客户提供优质产品是责无旁贷的。因此,即使是为了提高生产效率进行改善,也不能忽略品质的保证。
①在生产中铸就品质
要认为“后工序就是客户”,绝对不让不良品流到后工序
在设备、工装上装FP(控制装置)
②进行标准作业就是为了确保品质
反过来说,要为了确保需求品的品质而做成标准作业
③为了确保品质,一旦发现不良品需要停线的话,一定要停。
经常会听到这样的话“减少了工数之后,不良率上升了”,这种情况是因为作业量增加,进行工数改善时连必要的操作都给省掉了的缘故。
就算是要追求效率最大化,也不能省掉必要的作业。若正常情况下不能进行该作业,即使停线做,也要完成。
④对是否过分强调品质的想法的纠正
不会因为我进行了10次质检,卖价就会高一些。
我是不是对同一项目检查次数过多
3-3-2.改善时对安全问题的认识
做浪费的、多余的、勉强的作业或是让别人做这类作业是会造成灾害的。也就是说进行消除这类作业的改善就会确保安全生产,更加提高生产效率。
特别是在那些4S+S做得好的工场、间歇停线现象少的现场、遵守标准作业的现场,就会少一些灾害或不必要的损失。
3-3-3.从作业改善到设备改善
改善主要分为2大类
1、作业改善:
①决定作业规则(标准作业化)
②持续进行工艺分配
③改变物品的放置地点
④作业动作的改善
⑤实施组织结构的改善
2、设备改善:
①引入机器人、自动加工机器等
②手工作业的自动化
③设备、工装等的改善
TPS推进改善时,一定要首先彻底的进行作业改善。
在推进作业改善阶段,设备改善是无论如何都有必要的,所以步行考虑进行工装改良、设置制动器等“辅助性手段”。
‹在进行设备改善时的问题点›
①进行设备改善需要费用
目的是降低成本:若进行作业改善也能达到同样目的,就不需要花高额费用进行设备改善。(当然有时候是为了增加设备,那肯定是要花钱了.)
②没有改善的价值
若设备改善失败,那就是白花钱了
但是,若作业改善失败,还能很简单的挽回损失
③在进行作业改善之前进行设备改善,失败可能性很大
因为对换产和刀具交换作业未进行标准化(设备能力未完全发挥),所以错误认为设备能力不够,而购置自动化机器的例子很多。
3-3-4.省人化和省力化
有很多这样的例子:为了省人而进行设备投资,结果呢,人抽不出来。那样仅仅是省力化,那部分投资转化成了增加的成本。要以一人工为单位来省人,必须从一开始就要将实现降成本这一目的放如脑中。
3-4.引入JIT的步骤
以上都是说的以提高生产效率为目的的改善步骤,现在具体说明引入作为改善基盘的JIT的步骤。
(1) 引入步骤
①引入4S+S
②生产流程化
•整流化 •流水线化 •让多面手操作多工位
③小批量化
•改善换产
④引入标准作业
•规定节拍时间(循环时间即实际节拍),以此进行工艺平衡
⑤生产的平准化
⑥引入看板(生产组织结构的导入)
大多数人一看就以为首先就要“引入看板”,但在一些条件尚不具备的工场,单纯的导入可能会使生产结构变得更复杂,最后也会导致看板体系解体。所有必须按照顺序,在基本条件具备之后再引入。
(2) 开展顺序
分供方→前工序 →本工序→后工序→发货→客户
在引入时,要从发货和总装工序开始从后往前顺序开展。但是,前工序的管理监督人员也不宁那个说后工序的问题尚未清理就抱着双手旁观,前工序也应该积极的引入为后工序扫除障碍。
---------------------------------------------------------
阅读完此文章您有什么想法?问题?疑问?建议?意见?想和一起阅读此文的其他益友互动交流?想和我们的精益咨询专家探讨?
您可以1.【直接回复我们】
2.加【互动Q群】
3.到【微社区】
三个方式参与互动
---------------------------------------------------------
如果您觉得有用,请分享给您的朋友和同事,您的支持是我们努力的动力!!!
----------------------------------------------------------
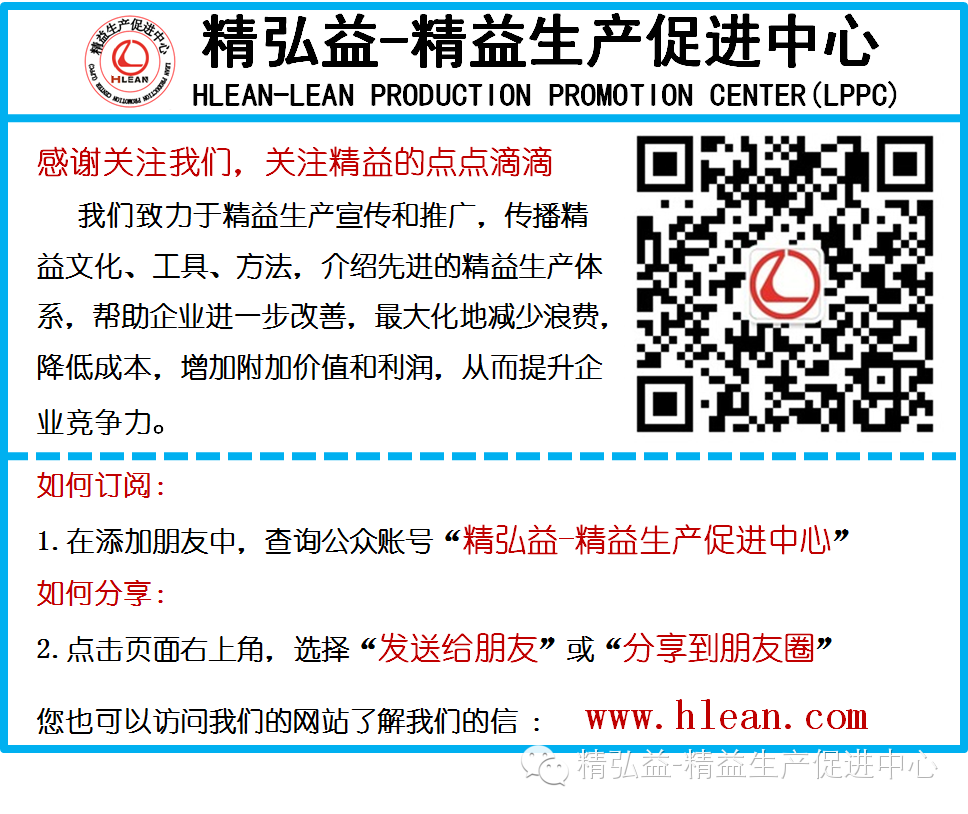
3-3.改善时的注意点
3-3-1.改善时对质量问题的认识
作为生产性企业,向客户提供优质产品是责无旁贷的。因此,即使是为了提高生产效率进行改善,也不能忽略品质的保证。
①在生产中铸就品质
要认为“后工序就是客户”,绝对不让不良品流到后工序
在设备、工装上装FP(控制装置)
②进行标准作业就是为了确保品质
反过来说,要为了确保需求品的品质而做成标准作业
③为了确保品质,一旦发现不良品需要停线的话,一定要停。
经常会听到这样的话“减少了工数之后,不良率上升了”,这种情况是因为作业量增加,进行工数改善时连必要的操作都给省掉了的缘故。
就算是要追求效率最大化,也不能省掉必要的作业。若正常情况下不能进行该作业,即使停线做,也要完成。
④对是否过分强调品质的想法的纠正
不会因为我进行了10次质检,卖价就会高一些。
我是不是对同一项目检查次数过多
3-3-2.改善时对安全问题的认识
做浪费的、多余的、勉强的作业或是让别人做这类作业是会造成灾害的。也就是说进行消除这类作业的改善就会确保安全生产,更加提高生产效率。
特别是在那些4S+S做得好的工场、间歇停线现象少的现场、遵守标准作业的现场,就会少一些灾害或不必要的损失。
3-3-3.从作业改善到设备改善
改善主要分为2大类
1、作业改善:
①决定作业规则(标准作业化)
②持续进行工艺分配
③改变物品的放置地点
④作业动作的改善
⑤实施组织结构的改善
2、设备改善:
①引入机器人、自动加工机器等
②手工作业的自动化
③设备、工装等的改善
TPS推进改善时,一定要首先彻底的进行作业改善。
在推进作业改善阶段,设备改善是无论如何都有必要的,所以步行考虑进行工装改良、设置制动器等“辅助性手段”。
‹在进行设备改善时的问题点›
①进行设备改善需要费用
目的是降低成本:若进行作业改善也能达到同样目的,就不需要花高额费用进行设备改善。(当然有时候是为了增加设备,那肯定是要花钱了.)
②没有改善的价值
若设备改善失败,那就是白花钱了
但是,若作业改善失败,还能很简单的挽回损失
③在进行作业改善之前进行设备改善,失败可能性很大
因为对换产和刀具交换作业未进行标准化(设备能力未完全发挥),所以错误认为设备能力不够,而购置自动化机器的例子很多。
3-3-4.省人化和省力化
有很多这样的例子:为了省人而进行设备投资,结果呢,人抽不出来。那样仅仅是省力化,那部分投资转化成了增加的成本。要以一人工为单位来省人,必须从一开始就要将实现降成本这一目的放如脑中。
3-4.引入JIT的步骤
以上都是说的以提高生产效率为目的的改善步骤,现在具体说明引入作为改善基盘的JIT的步骤。
(1) 引入步骤
①引入4S+S
②生产流程化
•整流化 •流水线化 •让多面手操作多工位
③小批量化
•改善换产
④引入标准作业
•规定节拍时间(循环时间即实际节拍),以此进行工艺平衡
⑤生产的平准化
⑥引入看板(生产组织结构的导入)
大多数人一看就以为首先就要“引入看板”,但在一些条件尚不具备的工场,单纯的导入可能会使生产结构变得更复杂,最后也会导致看板体系解体。所有必须按照顺序,在基本条件具备之后再引入。
(2) 开展顺序
分供方→前工序 →本工序→后工序→发货→客户
在引入时,要从发货和总装工序开始从后往前顺序开展。但是,前工序的管理监督人员也不宁那个说后工序的问题尚未清理就抱着双手旁观,前工序也应该积极的引入为后工序扫除障碍。
---------------------------------------------------------
阅读完此文章您有什么想法?问题?疑问?建议?意见?想和一起阅读此文的其他益友互动交流?想和我们的精益咨询专家探讨?
您可以1.【直接回复我们】
2.加【互动Q群】
3.到【微社区】
三个方式参与互动
---------------------------------------------------------
如果您觉得有用,请分享给您的朋友和同事,您的支持是我们努力的动力!!!
----------------------------------------------------------