效率提升技术
现在市场竞争越来越激烈,印制板组装厂要在这样的环境中立于不败之地,首要一点就是要降低其生产成本。而要实现这一目标,最主要的方法就是通过提高生产线的生产效率来实现。本文结合笔者工作实际探讨一些提高SMT生产线效率的方法和措施。
1、情况介绍
以烽火通信公司电装车间一条环球SMT生产线为研究对象,该生产线由一台DEK265、一台HSP4796L高速转塔贴片机、一台GSM1高精度贴片机和BTU回流炉组成。虽然一条SMT生产线由多台设备组成,但对SMT生产线效率影响最大的是贴片机。由于后面叙述的生产线平衡内容是关于这两类贴片机的,因此需要加以介绍。
HSP4796为转塔结构,采用十六个一组的旋转贴片头,每个贴片头上有五种不同吸嘴,两个料台,每个料站平台上可安装最多80种元件(8mm),贴装速度0.10s片,可贴装0201~钽电容、小型SOP等。
GSM1为拱架式结构,安装了新型Flex Jet贴装头,同以往贴装头相比,进行了以下一系列改进:把每个CCD摄像机内至到每个贴装头里,各自独立,以往的4 Spindle Nozzle已进化成7 Spindle Nozzle;把这样的7个贴装头都装设在贴装平台系统上,并行运行,最快贴装速度可达到1万片小时。
GSM1可使用卷带(tape)、条式(stick)、华夫盘(tray)各种类型的元件包装,而HSP4796L只能使用卷带。
目前已经总结相关方法和措施,并已经开始实施,大幅度提升生产效率。主要方法和措施如下:(1)PCB设计工艺;(2)生产线平衡;(3)设备程序优化;(4)管理措施;(5)提高新程序编制准确度;(6)良好的设备监控及维护;本文将在后面分别加以详细介绍。
2、PCB工艺设计
具有良好设计工艺的PCB可以提高生产效率,可以考虑以下一些因素:
(1)采用拼板设计。若PCB面积比较小,为了充分利用板材、高效率地制造、安装、调试SMA(表面贴装组件),往往将几块相同或者不同的PCB拼在一起成为一个大的版面,如图1所示。例如设计双面贴装不进行波峰焊的印制板时,可采用双数拼板正反面各半,两面图形按相同的排列方式可以提高设备利用率,节约生产准备费用和时间。
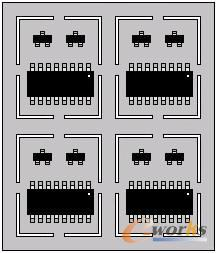
图1 拼板设计可提高生产效率
(2)元件布局尽可能集中整齐,类型相似的元件应该以相同的方向排列在板上,如图2所示,可减少贴装头的移动距离,提高生产效率。同时有规则的排列方便检查,并利于散热和焊接工艺的优化。
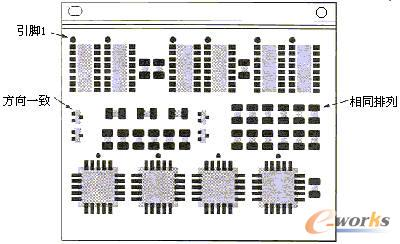
图2 相似元件的排列
(3)应考虑尽可能减少生产流程。两面有贴片元件考虑能否集中到一面。
3、生产线平衡
通常一条SMT生产线由一台高速贴片机和一台高精度贴片机组成,当两台贴片机生产时间相等且最小时,则整条生产线发挥出了最大产能。但这只是一种理想状态,实际会受很多因素影响。我们的目标尽可能合理分配元件,实现两台机器间的平衡。我们在初次分配每台设备的贴装元件数量时,往往会出现贴装时间差距较大,这就需要根据每台设备的贴装时间,对生产线上所有设备的生产负荷进行调整,将贴装时间较长设备上的部分元件移一部分到另一台设备上,以实现负荷分配平衡。另外在分配元件时还要注意以下因素:
(1)尽量不要将降速的元件(如钽电容、SOP等)分配到HSP上,避免由于少数几个元件导致旋转头整体降速,影响生产效率。
(2)根据每台贴片机能贴装的元件类型进行分配。例如,细间距元件给GSM,片式元件给HSP4796L。
(3)同时需考虑的另外一个问题是元件的包装形式,条式和华夫盘式元件只能用GSM来贴装。
4、设备程序优化
4.1 转塔机HSP4796L
其结构如图3所示,其工作时供料器平台可左右移动到吸取元件所在的料槽位置上,旋转贴片头顺时针旋转吸取元件,X-Y工作台可上下左右移动到贴装元件所在位置上。优化原则如下:
(1)两相临贴片元件位置最近(最短路径法)。减少X-Y工作台移动距离。
(2)两料位移动最小。减少料台移动时间。
(3)先贴快速元件,后贴慢速元件。避免慢速元件对整个头部旋转速度的影响。
所以在程序优化或者实施更改后要检查是否符合上述条件,若不符合则对贴装步骤进行调整。
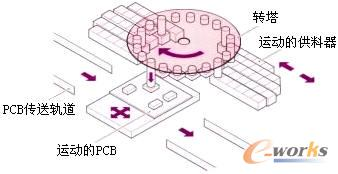
图3 HSP4796L结构
4.2 高精度贴片机GSM1
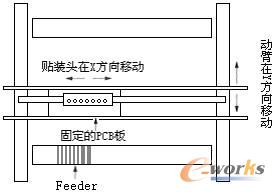
图4 GSM1结构
GSM1结构如图4所示,相比较于高速机,高精度贴片机程序编制更为复杂,制约的条件也更多。在GSM1贴片机程序优化时需要考虑的因素有:
(1)尽量不换吸嘴和少换吸嘴。目前GSM1实施不换吸嘴程序优化,平均程序效率提升幅度在5%-10%左右。另外可减少对机器头部的磨损。
(2)元件较多的Feeder离PCB最近,减少吸嘴移动行程。
(3)尽量实现同时吸取。使用多的元件可把放置Feeder数目由一个改为多个,可使元件同时吸着,缩短吸取时间,提高生产效率。
(4)提高元件识别效率。GSM1贴片机采用两套视觉对中系统,分别为位于机器后侧的仰视摄像机和机器头部的摄像机,仰视摄像机分辨率为4mil,主要用来识别大尺寸元件,头部摄像机分辨率为2.6mil,识别元件尺寸一般不应超过20mm,可实现飞行对中。这两套视觉对中系统结合在一起,确保了GSM1能高速而又准确地处理各种类型的元件。4mil摄像机所能处理的最小引脚宽度为0.203mm,针对33.358mm以下尺寸(例如QFP208)可一次成像,而对大于33.358mm尺寸的元件(例如QFP240)会采取四次照相合成的方法来增大照相面积的目的,先分别照四边,然后合成一个整个的器件,但所花费的时间将会成倍增长。了解到这些,在编程时应注意尽量避免将大于33.358mm尺寸的元件与小尺寸元件放在同一个循环中,这将影响到小尺寸元件的识别速度。
(5) 减少等待华夫盘元件时间。主要由于华夫盘供料速度跟不上吸取速度,调整贴装步骤,在吸取华夫盘元件前先吸取其它的元件。
(6)每个循环尽量满负荷,减少吸取次数。
(7)在一个循环过程中,尽量只从正面或后面的料站上取料,以减少贴装头移动距离。
有些原则在优化程序时会发生矛盾,这就需要进行折中考虑,以选出最佳优化方案来。
5、实施严格有效的管理措施
SMT设备是机电一体化的精密设备,在工作中实行严格有效的管理措施是提高SMT生产线效率的一个重要办法。我们采取的主要措施有:
(1)提前将要补充的元件装在备用送料器上,缩短换料时间;
(2)生产线装配前面批号产品的同时,提前做好生产线下一批号产品的准备工作等等。
(3)加强对操作员工的培训。SMT生产线属大生产流水线,产值是以秒来进行计算的。而生产的流畅性和产品的质量除设备与环境因素外,人的因素占有极为重要的成分。例如若操作员对设备很熟悉,那么在生产过程中排除问题所花费时间较少,也可节约生产时间,提高生产效率。所以我们格外重视对员工的培训,除了定期进行专业技能培训外,我们还以一些专业SMT书刊为教材组织员工学习,培养对SMT的热爱,提高每个人的综合业务水平。
(4)实施不停机换料。针对一些大批量产品, HSP4796L两个料台同时启用,减少换料停机时间。GSM1或者AC系列机器使用量较多的元件使用多个供料器,在一个供料器上元件用完时会自动转到另一供料器上取料,这时可取出空供料器进行元件补充。
6、提高新程序编制准确度,缩短调机时间
重点关注元件角度、封装、华夫盘设置参数等。
(1)关注元件角度。大多数PCB设计软件定义的贴片元件角度与烽火公司SMT设备程序定义的角度存在偏差,例如芯片、不规则方向阻容元件、排阻、二极管等(见表1),每次在一个新产品贴片程序编制过程中都需要一个个手工核对元件角度。如果元件数目较多,核对过程将非常耗时。
表1 烽火公司SMT设备与PCB设计软件定义元件角度对比
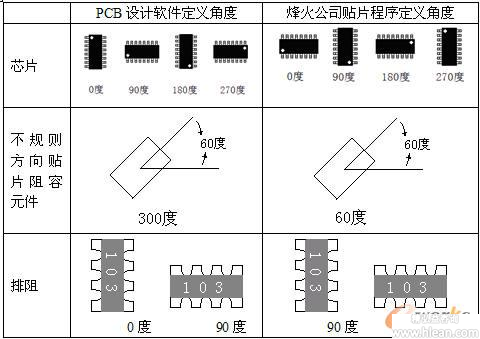
通常这种偏差是有规律可循的,例如芯片,烽火公司贴片程序定义角度与PCB设计软件定义的角度统一偏差-90度,可以用EXCEL等通用字处理软件来处理,但较为繁琐。为解决这个问题,我专门开发了DPS(Data Preparation System)数据准备软件,可在数秒钟之内完成所有型号元件角度修正,即准确又快速,目前该软件在我公司新产品数据准备过程中得到广泛应用,提高了程序编制的准确度。
(2)核对芯片封装。GSM1编程软件UPS可显示贴片程序的图形模式(如图5),非常接近实际,可用来与元件实物进行比较,非常方便核对,避免封装出错导致新产品调机时间延长。
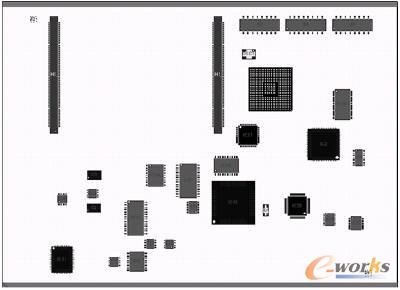
图5 GSM1编程软件UPS可显示贴片程序的图形模式
7、良好的设备监控及维护
SMT设备进行定期检验与保养也是保证其充分发挥其功效的有力措施之一。很多公司由于生产任务繁重,在生产过程中往往会忽视这一点。一旦设备因故障不能正常生产时,其停工所造成的损失要远远大于对设备定期停机检验与保养的费用。因此必须强调对设备定期进行科学的检验与保养,加强对设备上一些易损件的定期检查,包括滤芯、吸嘴、照明电源、切刀等,若出现情况及时更换并采购,确保机器处于良好状态下,避免机器由于不正常的工作状态导致生产效率下降,例如抛料率过高致使部分吸嘴被屏蔽掉。
8、结论
SMT生产需要高的投入,但如果管理与使用得法,并注意笔者在上面提到的几个方面,我们将会充分挖掘SMT生产线的生产潜力,提高生产效率,在几年之内就会收回全部的投资,实现“高投入、高产出”。
1、情况介绍
以烽火通信公司电装车间一条环球SMT生产线为研究对象,该生产线由一台DEK265、一台HSP4796L高速转塔贴片机、一台GSM1高精度贴片机和BTU回流炉组成。虽然一条SMT生产线由多台设备组成,但对SMT生产线效率影响最大的是贴片机。由于后面叙述的生产线平衡内容是关于这两类贴片机的,因此需要加以介绍。
HSP4796为转塔结构,采用十六个一组的旋转贴片头,每个贴片头上有五种不同吸嘴,两个料台,每个料站平台上可安装最多80种元件(8mm),贴装速度0.10s片,可贴装0201~钽电容、小型SOP等。
GSM1为拱架式结构,安装了新型Flex Jet贴装头,同以往贴装头相比,进行了以下一系列改进:把每个CCD摄像机内至到每个贴装头里,各自独立,以往的4 Spindle Nozzle已进化成7 Spindle Nozzle;把这样的7个贴装头都装设在贴装平台系统上,并行运行,最快贴装速度可达到1万片小时。
GSM1可使用卷带(tape)、条式(stick)、华夫盘(tray)各种类型的元件包装,而HSP4796L只能使用卷带。
目前已经总结相关方法和措施,并已经开始实施,大幅度提升生产效率。主要方法和措施如下:(1)PCB设计工艺;(2)生产线平衡;(3)设备程序优化;(4)管理措施;(5)提高新程序编制准确度;(6)良好的设备监控及维护;本文将在后面分别加以详细介绍。
2、PCB工艺设计
具有良好设计工艺的PCB可以提高生产效率,可以考虑以下一些因素:
(1)采用拼板设计。若PCB面积比较小,为了充分利用板材、高效率地制造、安装、调试SMA(表面贴装组件),往往将几块相同或者不同的PCB拼在一起成为一个大的版面,如图1所示。例如设计双面贴装不进行波峰焊的印制板时,可采用双数拼板正反面各半,两面图形按相同的排列方式可以提高设备利用率,节约生产准备费用和时间。
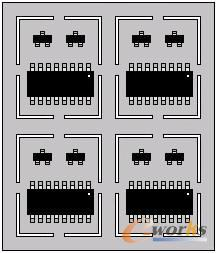
图1 拼板设计可提高生产效率
(2)元件布局尽可能集中整齐,类型相似的元件应该以相同的方向排列在板上,如图2所示,可减少贴装头的移动距离,提高生产效率。同时有规则的排列方便检查,并利于散热和焊接工艺的优化。
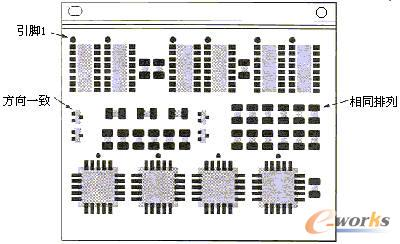
图2 相似元件的排列
(3)应考虑尽可能减少生产流程。两面有贴片元件考虑能否集中到一面。
3、生产线平衡
通常一条SMT生产线由一台高速贴片机和一台高精度贴片机组成,当两台贴片机生产时间相等且最小时,则整条生产线发挥出了最大产能。但这只是一种理想状态,实际会受很多因素影响。我们的目标尽可能合理分配元件,实现两台机器间的平衡。我们在初次分配每台设备的贴装元件数量时,往往会出现贴装时间差距较大,这就需要根据每台设备的贴装时间,对生产线上所有设备的生产负荷进行调整,将贴装时间较长设备上的部分元件移一部分到另一台设备上,以实现负荷分配平衡。另外在分配元件时还要注意以下因素:
(1)尽量不要将降速的元件(如钽电容、SOP等)分配到HSP上,避免由于少数几个元件导致旋转头整体降速,影响生产效率。
(2)根据每台贴片机能贴装的元件类型进行分配。例如,细间距元件给GSM,片式元件给HSP4796L。
(3)同时需考虑的另外一个问题是元件的包装形式,条式和华夫盘式元件只能用GSM来贴装。
4、设备程序优化
4.1 转塔机HSP4796L
其结构如图3所示,其工作时供料器平台可左右移动到吸取元件所在的料槽位置上,旋转贴片头顺时针旋转吸取元件,X-Y工作台可上下左右移动到贴装元件所在位置上。优化原则如下:
(1)两相临贴片元件位置最近(最短路径法)。减少X-Y工作台移动距离。
(2)两料位移动最小。减少料台移动时间。
(3)先贴快速元件,后贴慢速元件。避免慢速元件对整个头部旋转速度的影响。
所以在程序优化或者实施更改后要检查是否符合上述条件,若不符合则对贴装步骤进行调整。
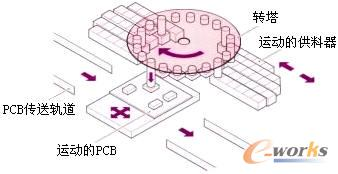
图3 HSP4796L结构
4.2 高精度贴片机GSM1
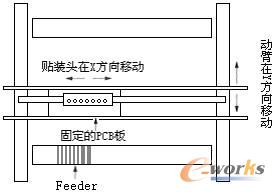
图4 GSM1结构
GSM1结构如图4所示,相比较于高速机,高精度贴片机程序编制更为复杂,制约的条件也更多。在GSM1贴片机程序优化时需要考虑的因素有:
(1)尽量不换吸嘴和少换吸嘴。目前GSM1实施不换吸嘴程序优化,平均程序效率提升幅度在5%-10%左右。另外可减少对机器头部的磨损。
(2)元件较多的Feeder离PCB最近,减少吸嘴移动行程。
(3)尽量实现同时吸取。使用多的元件可把放置Feeder数目由一个改为多个,可使元件同时吸着,缩短吸取时间,提高生产效率。
(4)提高元件识别效率。GSM1贴片机采用两套视觉对中系统,分别为位于机器后侧的仰视摄像机和机器头部的摄像机,仰视摄像机分辨率为4mil,主要用来识别大尺寸元件,头部摄像机分辨率为2.6mil,识别元件尺寸一般不应超过20mm,可实现飞行对中。这两套视觉对中系统结合在一起,确保了GSM1能高速而又准确地处理各种类型的元件。4mil摄像机所能处理的最小引脚宽度为0.203mm,针对33.358mm以下尺寸(例如QFP208)可一次成像,而对大于33.358mm尺寸的元件(例如QFP240)会采取四次照相合成的方法来增大照相面积的目的,先分别照四边,然后合成一个整个的器件,但所花费的时间将会成倍增长。了解到这些,在编程时应注意尽量避免将大于33.358mm尺寸的元件与小尺寸元件放在同一个循环中,这将影响到小尺寸元件的识别速度。
(5) 减少等待华夫盘元件时间。主要由于华夫盘供料速度跟不上吸取速度,调整贴装步骤,在吸取华夫盘元件前先吸取其它的元件。
(6)每个循环尽量满负荷,减少吸取次数。
(7)在一个循环过程中,尽量只从正面或后面的料站上取料,以减少贴装头移动距离。
有些原则在优化程序时会发生矛盾,这就需要进行折中考虑,以选出最佳优化方案来。
5、实施严格有效的管理措施
SMT设备是机电一体化的精密设备,在工作中实行严格有效的管理措施是提高SMT生产线效率的一个重要办法。我们采取的主要措施有:
(1)提前将要补充的元件装在备用送料器上,缩短换料时间;
(2)生产线装配前面批号产品的同时,提前做好生产线下一批号产品的准备工作等等。
(3)加强对操作员工的培训。SMT生产线属大生产流水线,产值是以秒来进行计算的。而生产的流畅性和产品的质量除设备与环境因素外,人的因素占有极为重要的成分。例如若操作员对设备很熟悉,那么在生产过程中排除问题所花费时间较少,也可节约生产时间,提高生产效率。所以我们格外重视对员工的培训,除了定期进行专业技能培训外,我们还以一些专业SMT书刊为教材组织员工学习,培养对SMT的热爱,提高每个人的综合业务水平。
(4)实施不停机换料。针对一些大批量产品, HSP4796L两个料台同时启用,减少换料停机时间。GSM1或者AC系列机器使用量较多的元件使用多个供料器,在一个供料器上元件用完时会自动转到另一供料器上取料,这时可取出空供料器进行元件补充。
6、提高新程序编制准确度,缩短调机时间
重点关注元件角度、封装、华夫盘设置参数等。
(1)关注元件角度。大多数PCB设计软件定义的贴片元件角度与烽火公司SMT设备程序定义的角度存在偏差,例如芯片、不规则方向阻容元件、排阻、二极管等(见表1),每次在一个新产品贴片程序编制过程中都需要一个个手工核对元件角度。如果元件数目较多,核对过程将非常耗时。
表1 烽火公司SMT设备与PCB设计软件定义元件角度对比
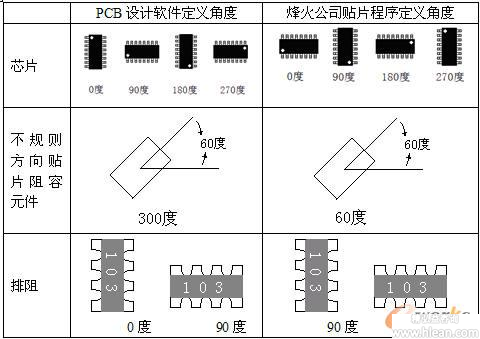
通常这种偏差是有规律可循的,例如芯片,烽火公司贴片程序定义角度与PCB设计软件定义的角度统一偏差-90度,可以用EXCEL等通用字处理软件来处理,但较为繁琐。为解决这个问题,我专门开发了DPS(Data Preparation System)数据准备软件,可在数秒钟之内完成所有型号元件角度修正,即准确又快速,目前该软件在我公司新产品数据准备过程中得到广泛应用,提高了程序编制的准确度。
(2)核对芯片封装。GSM1编程软件UPS可显示贴片程序的图形模式(如图5),非常接近实际,可用来与元件实物进行比较,非常方便核对,避免封装出错导致新产品调机时间延长。
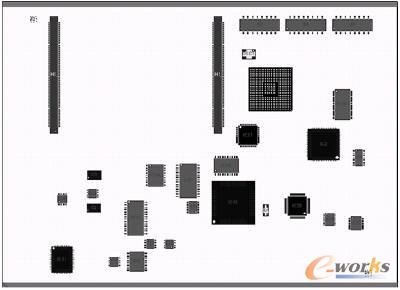
图5 GSM1编程软件UPS可显示贴片程序的图形模式
7、良好的设备监控及维护
SMT设备进行定期检验与保养也是保证其充分发挥其功效的有力措施之一。很多公司由于生产任务繁重,在生产过程中往往会忽视这一点。一旦设备因故障不能正常生产时,其停工所造成的损失要远远大于对设备定期停机检验与保养的费用。因此必须强调对设备定期进行科学的检验与保养,加强对设备上一些易损件的定期检查,包括滤芯、吸嘴、照明电源、切刀等,若出现情况及时更换并采购,确保机器处于良好状态下,避免机器由于不正常的工作状态导致生产效率下降,例如抛料率过高致使部分吸嘴被屏蔽掉。
8、结论
SMT生产需要高的投入,但如果管理与使用得法,并注意笔者在上面提到的几个方面,我们将会充分挖掘SMT生产线的生产潜力,提高生产效率,在几年之内就会收回全部的投资,实现“高投入、高产出”。